課程設(shè)計(jì)說明書夾具.doc
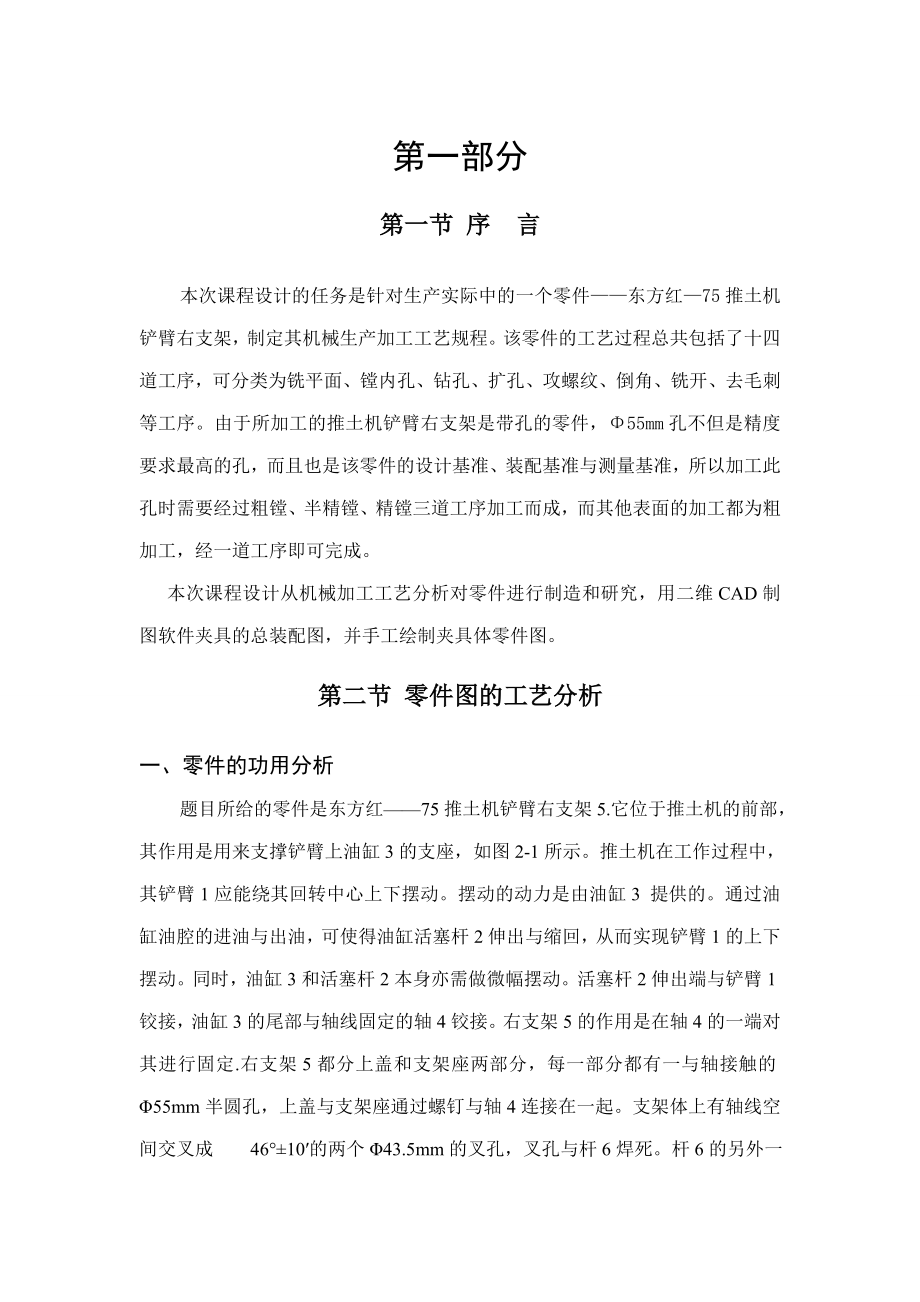


《課程設(shè)計(jì)說明書夾具.doc》由會(huì)員分享,可在線閱讀,更多相關(guān)《課程設(shè)計(jì)說明書夾具.doc(41頁(yè)珍藏版)》請(qǐng)?jiān)谘b配圖網(wǎng)上搜索。
1、第一部分第一節(jié) 序 言 本次課程設(shè)計(jì)的任務(wù)是針對(duì)生產(chǎn)實(shí)際中的一個(gè)零件東方紅75推土機(jī)鏟臂右支架,制定其機(jī)械生產(chǎn)加工工藝規(guī)程。該零件的工藝過程總共包括了十四道工序,可分類為銑平面、鏜內(nèi)孔、鉆孔、擴(kuò)孔、攻螺紋、倒角、銑開、去毛刺等工序。由于所加工的推土機(jī)鏟臂右支架是帶孔的零件,55mm孔不但是精度要求最高的孔,而且也是該零件的設(shè)計(jì)基準(zhǔn)、裝配基準(zhǔn)與測(cè)量基準(zhǔn),所以加工此孔時(shí)需要經(jīng)過粗鏜、半精鏜、精鏜三道工序加工而成,而其他表面的加工都為粗加工,經(jīng)一道工序即可完成。本次課程設(shè)計(jì)從機(jī)械加工工藝分析對(duì)零件進(jìn)行制造和研究,用二維CAD制圖軟件夾具的總裝配圖,并手工繪制夾具體零件圖。第二節(jié) 零件圖的工藝分析一、
2、零件的功用分析 題目所給的零件是東方紅75推土機(jī)鏟臂右支架5.它位于推土機(jī)的前部,其作用是用來支撐鏟臂上油缸3的支座,如圖2-1所示。推土機(jī)在工作過程中,其鏟臂1應(yīng)能繞其回轉(zhuǎn)中心上下擺動(dòng)。擺動(dòng)的動(dòng)力是由油缸3 提供的。通過油缸油腔的進(jìn)油與出油,可使得油缸活塞桿2伸出與縮回,從而實(shí)現(xiàn)鏟臂1的上下擺動(dòng)。同時(shí),油缸3和活塞桿2本身亦需做微幅擺動(dòng)?;钊麠U2伸出端與鏟臂1鉸接,油缸3的尾部與軸線固定的軸4鉸接。右支架5的作用是在軸4的一端對(duì)其進(jìn)行固定.右支架5都分上蓋和支架座兩部分,每一部分都有一與軸接觸的55mm半圓孔,上蓋與支架座通過螺釘與軸4連接在一起。支架體上有軸線空間交叉成 4610的兩個(gè)43
3、.5mm的叉孔,叉孔與桿6焊死。桿6的另外一端與一塊鋼板7焊接在一起,鋼板7與推土機(jī)底盤鉚接,最終把軸4與底盤固定在一起。從零件的實(shí)際功用看,右支架5的主要作用是連接與緊固。1-鏟臂 2-活塞桿 3-油缸 4-軸 5-右支架 6-桿 7-鋼板圖2-1 右支架功用是意圖二、零件的工藝分析從零件圖上可以看出,標(biāo)有表面粗糙度符號(hào)的表面有平面、退刀槽、內(nèi)孔等。其中,表面粗糙度要求最高的是55mm孔,公差等級(jí)達(dá)到IT8級(jí),表面粗糙度為Ra1.6m。該孔是右支架的主要設(shè)計(jì)基準(zhǔn)。從表面間的位置精度要求來看,A、B兩端面(即前、后兩端面)應(yīng)與55mm孔軸線垂直,兩個(gè)43.5mm孔的軸線應(yīng)垂直與55mm孔軸線,
4、且兩43.5mm軸線的夾角應(yīng)為4610,夾角頂點(diǎn)在55mm孔的軸線上。從工藝上看,43.5mm孔的軸線對(duì)55mm孔的軸線的垂直度要求為 0.2100,相當(dāng)于公差等級(jí)10級(jí),可以通過使用專用夾具來保證。55mm孔公差等級(jí)為IT8級(jí),表面粗糙度為Ra1.6m,可通過精鏜保證。平面A、B用于軸的軸向定位,小凸臺(tái)C平面與B平面在同一平面上,在零件的工作過程中不起作用。由于工藝凸臺(tái)C平面面積較小,為保證鑄件質(zhì)量,將B、C平面取為澆鑄的底面位置,將A面作為澆鑄時(shí)的頂面位置。 對(duì)右支架零件圖進(jìn)行工藝審核后,可知該零件圖視圖正確、完整、尺寸、公差及技術(shù)要求齊全,加工要求合理,零件的結(jié)構(gòu)工藝性較好。機(jī)械加工工序
5、的安排一、確定零件的生產(chǎn)類型按設(shè)計(jì)任務(wù)書,東方紅75推土機(jī)年產(chǎn)量為4500臺(tái)/年,其上有左、右支架各一件。若右支架備品率為8%,機(jī)械加工廢品率為1%,則該零件的年生產(chǎn)綱領(lǐng)為4500(1+8+1)件/年=4905件/年 (3-1)可見,右鏟臂支架的年生產(chǎn)量為4905件。推土機(jī)鏟臂支架可看成獨(dú)立的一部分,屬輕型機(jī)械。因此,根據(jù)表,有生產(chǎn)綱領(lǐng)與生產(chǎn)類型的關(guān)系可確定該零件的生產(chǎn)為中批生產(chǎn),其毛坯制造、加工設(shè)備及工藝裝備的選擇應(yīng)呈現(xiàn)中批生產(chǎn)的工藝特點(diǎn),如多采用通用設(shè)備配以專用的工藝裝備等。二、確定毛坯制造形式 由該零件的功用及推土機(jī)的工作狀況知,鏟臂支架與連接支架上蓋與支架座的螺釘承受的都是沖擊性載荷,
6、故要求該支架材料應(yīng)具備較高的強(qiáng)度與抗沖擊能力。因此,原設(shè)計(jì)單位選用了既滿足要求,價(jià)格有相對(duì)低廉的鑄鋼材料ZG310-570,因此可以確定毛坯的制造形式為鑄造。一般工程用鑄鋼的特性和應(yīng)用見表。由于該支架為成批生產(chǎn),由表可知,選擇砂型機(jī)器造型,鑄鋼件的公差等級(jí)為CT9級(jí)。該零件的形狀不是十分復(fù)雜,因此毛坯的形狀與零件的形狀應(yīng)盡量接近。由于在55mm孔的軸線方向上還有一個(gè)49mm孔,從減少加工余量考慮,此處的毛坯孔可以與55mm的毛坯孔一起鑄成階梯孔。2個(gè)43.5mm孔徑也較大,因此在鑄造時(shí)也應(yīng)鑄成出毛坯孔。三、選擇定位基準(zhǔn)定位基準(zhǔn)的選擇是工藝規(guī)程制定中的重要工作,它是工藝路線是否正確合理的前提。正
7、確與合理地選擇定位基準(zhǔn),可以確保加工質(zhì)量、縮短工藝過程、簡(jiǎn)化工藝裝備結(jié)構(gòu)與種類、提高生產(chǎn)率。 精基準(zhǔn)的選擇精基準(zhǔn)的選擇原則為:基準(zhǔn)重合原則、基準(zhǔn)統(tǒng)一原則、互為基準(zhǔn)原則、自為基準(zhǔn)原則??筛鶕?jù)以上原則進(jìn)行精基準(zhǔn)的選擇。右支架是帶孔的零件。55mm孔不但是精度要求最高的孔,而且也是零件的設(shè)計(jì)基準(zhǔn)。裝配基準(zhǔn)與測(cè)量基準(zhǔn)。為避免由于基準(zhǔn)不重合而產(chǎn)生的誤差,保證加工精度,應(yīng)選55mm孔為基準(zhǔn),即遵循“基準(zhǔn)重合”的原則。同時(shí)為了定位可靠,使加工過程穩(wěn)定、減小振動(dòng),還可選B、C平面為精基準(zhǔn)。即選55mm孔及地面B、工藝凸臺(tái)面C所構(gòu)成的組合平面作為精基準(zhǔn),以一個(gè)長(zhǎng)孔與一個(gè)大端面定位。為了避免過定位可采用55mm孔
8、一段短孔與端面的組合,或采用55mm孔長(zhǎng)孔與 55mm孔一小部分端面的組合??紤]到該零件精度不是太高以及加工時(shí)的穩(wěn)定性,最終選底面B和工藝凸臺(tái)C作為第一定位基準(zhǔn),限制三個(gè)自由度,55mm短孔作為第二定位基準(zhǔn),限制二個(gè)自由度。為了限制右支架繞55mm孔中心線的旋轉(zhuǎn)自由度,還可選二個(gè)43.5mm孔之一的外緣表面作為第三定位基準(zhǔn),在此設(shè)置一個(gè)擋銷。在右支架的加工過程中,該組合表面還可作為大部分工序的定位基準(zhǔn),加工其他的次要表面,體現(xiàn)了“基準(zhǔn)統(tǒng)一”的選擇原則。2 粗基準(zhǔn)的選擇粗基準(zhǔn)的選擇原則為:合理分配加工余量的原則、保證相互位置的要求的原則、便于裝夾的原則。55mm孔為重要表面,加工時(shí)要求余量小而均
9、勻,因此應(yīng)選擇該55mm長(zhǎng)孔為粗基準(zhǔn)。但此時(shí)的定位、夾緊裝置結(jié)構(gòu)復(fù)雜??紤]到該零件精度要求不是太高,可選底面B與工藝凸臺(tái)面C的組合表面作為粗基準(zhǔn),這樣可使定位和加緊方便、可靠。由于采用機(jī)械造型,鑄件有一定的精度,基本可以保證55mm孔的加工余量均勻。由上可看出,粗、精基準(zhǔn)選擇結(jié)果基本上是一致的,均選擇了底面B與工藝凸臺(tái)面C所構(gòu)成的組合表面。四、選擇加工方法 平面的加工平面的加工方法很多,有車、刨、銑、磨、拉等。對(duì)于本支架,面A與面B的粗糙度要求Ra12.5m,其距離尺寸100mm為未注公差尺寸。由表5-11,根據(jù) GB/T1804-2000規(guī)定,選用中等級(jí)m,相當(dāng)于IT13級(jí),故可考慮粗車或粗
10、端銑,但車削加工底面的工藝凸臺(tái)C時(shí)會(huì)出現(xiàn)斷續(xù)車削,沖擊較大,故選擇端銑加工方式。 孔及退刀槽的加工孔的加工方式有鉆、擴(kuò)、鏜、拉、磨等。對(duì)于已鑄出55mm孔和49mm孔的階梯型毛坯,可采取在車床上鏜孔的方式。原因之一是該零件的結(jié)構(gòu)緊湊,重量也不大,適用于車削加工;原因之二是該零件精度不是很高,使用車床鏜孔較為經(jīng)濟(jì)。對(duì)于49mm孔,其公差等級(jí)為IT14,退刀槽屬未注公差尺寸,兩孔都可一次鏜出。55mm孔的公差等級(jí)為IT8級(jí),表面粗糙度要求為Ra1.6m,可采取 粗鏜半精鏜精鏜的加工方式。對(duì)于右支架座上四個(gè)M20mm螺紋底孔及6個(gè)20mm孔,都屬于未注公差尺寸,可在實(shí)體上一次鉆出。對(duì)于二個(gè)43.5m
11、m孔,要求其軸線與55mm孔軸線垂直,且二個(gè)43.5孔軸線夾角成4610,考慮到毛坯上已有預(yù)鑄孔,可采取一次擴(kuò)孔實(shí)現(xiàn)。加工方法有兩種:用麻花鉆擴(kuò)孔; 用擴(kuò)孔鉆擴(kuò)孔。在實(shí)際生產(chǎn)中常用經(jīng)修磨的麻花鉆當(dāng)擴(kuò)孔鉆使用。由表5-12知鉆孔的公差等級(jí)為IT12IT13,可以滿足加工要求,故這里使用錐柄麻花鉆進(jìn)行擴(kuò)孔。 螺紋加工右支架座上4個(gè)M20mm螺紋孔應(yīng)采取攻螺紋的方式。在攻螺紋工序之前應(yīng)設(shè)置一道倒角工序,或在本工序中應(yīng)先設(shè)一道倒角工步,以避免折斷絲錐,使攻螺紋順利進(jìn)行。 零件的剖開右支架最終要分成上蓋與支架座兩部分,剖分面表面粗糙度要求為Ra12.5m,中心面應(yīng)通過55mm孔的軸線??衫眯妮S定位將其
12、一次或分兩次在銑床上用鋸片銑刀銑開。為使定位方便及使夾具的結(jié)構(gòu)簡(jiǎn)單采取在一個(gè)工序中分兩次安裝銑開的方法,即在臥銑刀桿上裝有兩把鋸片銑刀,分別用于銑開右支架的一半。五、制定工藝路線1)右支架零件的生產(chǎn)類型是中批量生產(chǎn),其工藝特點(diǎn)是盡量選用通用機(jī)床并配以專用夾具。在安排本零件工藝路線的過程中主要考慮了以下幾個(gè)方面:底面B與55mm孔一部分短孔為精基準(zhǔn),同時(shí)底面B也是粗基準(zhǔn),根據(jù)“先面后孔”和“基面先行”的原則,最先開始加工頂面A與底面B,底面B與工藝凸臺(tái)面C屬于同一平面,裝卡后一次加工。右支架加工表面中55mm孔精度最高,一切工序都是圍繞保證該孔的精度開安排。根據(jù)“先主后次”的原則,55mm孔應(yīng)安
13、排在工藝路線的前部進(jìn)行,但又不能一次加工到設(shè)計(jì)要求,否則在后續(xù)的工序中利用該表面定位加工一些次要表面時(shí),有可能損傷該表面。“先粗后精”是針對(duì)整個(gè)工藝路線而言的,而并非只對(duì)某一表面而言。對(duì)于55mm孔,它是其他次要表面的基準(zhǔn),必須先加工出來。在具體處理時(shí)可將 55mm孔半精加工后作為統(tǒng)一的精基準(zhǔn)來加工其他次要表面,待這些次要表面加工完成之后在對(duì)其精加工至圖樣要求。2)工藝路線安排如何安排工藝路線,一定要根據(jù)現(xiàn)場(chǎng)實(shí)際情況,具體情況具體分析。最終的工藝路線安排如下:工序05:粗銑頂面A 定位基準(zhǔn):底面B、工藝凸臺(tái)C面。工序10:粗細(xì)底面B、工藝凸臺(tái)C面 定位基準(zhǔn):頂面A。工序15:粗鏜49mm孔(工
14、步一)及退刀槽356mm(工步二) 定位基準(zhǔn):底面B、工藝凸臺(tái)C面及55mm毛坯孔。工序20:粗鏜55mm孔(工步一)及倒角C2(工步二) 定位基準(zhǔn):頂面A及49mm孔。工序25:半精鏜55mm孔 定位基準(zhǔn):頂面A及49mm孔。工序30:擴(kuò)243.5mm孔 定位基準(zhǔn):底面B、工藝凸臺(tái)C面、55mm孔及43.5mm孔外緣。工序35: 243.5mm倒角C2 定位基準(zhǔn):底面B、工藝凸臺(tái)C面、55mm孔及43.5mm孔外緣。工序40:鉆620mm孔 定位基準(zhǔn):底面B。工藝凸臺(tái)C面。55mm孔及一個(gè)43.5mm孔。工序45:鉆4M202螺紋底孔18mm 定位基準(zhǔn):底面B、工藝凸臺(tái)C面、55mm孔及一個(gè)
15、20mm孔。工序50:精鏜55mm孔(工步一)及倒角C2(工步二) 定位基準(zhǔn):頂面A及49mm孔。工序55;銑開(兩次安裝) 安裝一:銑開零件一側(cè) 定位基準(zhǔn):底面B、工藝凸臺(tái)C面、55mm孔及一個(gè)20mm孔。 安裝二:銑開零件另一側(cè) 定位基準(zhǔn):底面B、工藝凸臺(tái)C面、55mm孔及銑開的切口。工序60:擴(kuò)上蓋621mm孔 定位基準(zhǔn):剖分面、55mm半圓孔及一端面。工序65:4M202底孔倒角(工步一)、攻4M202支架座螺紋(工步二) 定位基準(zhǔn):55mm半圓孔、端面及一個(gè)20mm孔。工序70:去毛刺、清洗、檢驗(yàn)。六、確定毛坯余量及毛坯尺寸(一)確定加工余量該支架材料為ZG310-570,屈服強(qiáng)度=
16、310MPa,抗拉強(qiáng)度=570MPa,采用砂型機(jī)器造型,且為成批生產(chǎn)。由表5-2知,鑄鋼件采用砂型機(jī)器造型時(shí),鑄件尺寸公差為CT8CT12級(jí),此處選為CT9級(jí)。由表5-3選擇加工余量為H級(jí),根據(jù)機(jī)械加工后鑄件的最大輪廓尺寸有表5-4可查的各加工表面加工余量,如下表所示: 右支架各加工表面加工余量加工表面單邊余量/mm雙邊余量/mm備注55mm孔、 49mm孔3.06.0基本尺寸取孔軸向長(zhǎng)度尺寸101mm頂面A因鑄造頂面,故加大取4.0面A、面B為雙側(cè)均加工,并考慮鑄造情況,基本尺寸為101mm底面B3.02個(gè)43.5mm孔3.06.0基本尺寸為孔深尺寸68mm 零件重量約為7.4kg,加上加工
17、余量,經(jīng)過估算,毛坯重量約為9.5kg。(二)確定毛坯基本尺寸 加工表面的毛坯尺寸只需將零件尺寸加上相應(yīng)的加工余量即可,所得毛坯尺寸如下表所示:右支架毛坯尺寸零件尺寸/mm單邊加工余量/mm毛坯尺寸/mm101頂面A為4,底面B為3108553494934343.5337.5(三)確定毛坯尺寸公差由表5-3查得各鑄件加工尺寸公差如表4-3所示:表4-3 右支架鑄件加工尺寸公差毛坯尺寸/mm公差/mm按“對(duì)稱”標(biāo)注結(jié)果/mm1082.51.251081.25492.01491432.0143137.51.80.937.50.9(四)繪制毛坯簡(jiǎn)圖 右支架毛坯簡(jiǎn)圖七、工序設(shè)計(jì)(一)加工設(shè)備與工藝設(shè)備
18、的選擇1、選擇加工設(shè)備 選擇加工設(shè)備即選擇機(jī)床類型。其經(jīng)濟(jì)精度應(yīng)與零件表面的設(shè)計(jì)要求相適應(yīng),初步選定各工序機(jī)床如下:工序05、10銑平面:XA5032立式升降臺(tái)銑床,主要技術(shù)參數(shù)見表5-13;工序15、20、25、50鏜孔:由于加工的零件外輪廓尺寸不大,故宜在車床上鏜孔,選擇常用的CA6140臥式車床。同時(shí),由于使用時(shí)間長(zhǎng)短的不同,各機(jī)床的精度也不同,在選擇機(jī)床進(jìn)行粗、精加工工序時(shí)應(yīng)不同;工序30、35擴(kuò)孔、倒角:Z35搖臂鉆床,主要參數(shù)見表5-14;工序40、45 、60、65鉆孔、攻螺紋:Z3025搖臂鉆床,主要技術(shù)參數(shù)見 表5-14;工序55銑開:XA6132臥式銑床,主要技術(shù)參數(shù)見表5
19、-13;2、 選擇夾具對(duì)于成批生產(chǎn)的零件,大多數(shù)采用專用機(jī)床夾具。在保證加工質(zhì)量、操作方便、滿足高效的前提下,亦可部分采用通用夾具。本機(jī)械加工工藝規(guī)程中所有工序均采用了裝用機(jī)床夾具,需專門設(shè)計(jì)、制造。3、選擇刀具在右支架的加工中,采用了銑、鏜、鉆、擴(kuò)、攻螺紋等多種加工方式,與之相對(duì)應(yīng),初選道具的情況如下: 銑刀 工序05、10中頂面A、底面B采用端銑刀來進(jìn)行加工。工序05中要求銑削深度為=4mm,工序10要求銑削深度為=3mm,銑削寬度均為=94mm。根據(jù)表5-15,選用高速鋼鑲齒套式端銑刀。由表5-16知所需銑刀直徑為110130mm。查表5-17知,滿足加工要求的銑刀直徑d=125mm,孔
20、徑D=40mm,寬L=40mm,齒數(shù)z=14。工序55中銑開加工所用銑刀,根據(jù)工件尺寸,由表5-18知,選用中齒鋸片銑刀(GB6120-1996),直徑d=160mm,孔徑D=32mm,寬L=5mm,齒數(shù)z=48。 鏜刀 在車床上加工的工序,一般都選用硬質(zhì)合金刀具。加工鋼制零件可采用YT類硬質(zhì)合金,粗加工時(shí)用YT5,半精加工時(shí)用YT15精加工時(shí)用YT30,且均可采用=45,直徑為20mm的圓形鏜刀進(jìn)行加工。 鉆頭 從零件要求和加工經(jīng)濟(jì)性考慮,采用錐柄麻花鉆頭(GB 1438-2008)完成加工工序。工序30中,采用麻花鉆擴(kuò)孔,由表5-19知,選用d=43.5mm的高速鋼錐柄麻花鉆;工序35中,
21、采用锪鉆進(jìn)行倒角;工序40中,選用20mm的麻花鉆鉆6個(gè)20mm孔;工序45中,由表5-20知,鉆M20mm螺紋底孔的鉆頭直徑為18mm,由表5-84知,選用d=18mm的高速鋼錐柄麻花鉆。 絲錐 根據(jù)表5-21可知,選用M202細(xì)柄機(jī)用絲錐(摘自GB 3464-2007)完成攻螺紋工序。4、 選擇量具 選擇連狙的原則是根據(jù)被測(cè)量的對(duì)象的要求,在滿足測(cè)量精度的前提下,盡量選用操作方便、測(cè)量效率高的量具。本零件屬于成批生產(chǎn),一般采用通用量具。(2) 確定工序尺寸確定工序尺寸時(shí),對(duì)于加工加工精度較低的表面,只需粗加工工序就能保證設(shè)計(jì)要求,將設(shè)計(jì)尺寸作為工序尺寸即可,上下偏差也按設(shè)計(jì)規(guī)定。當(dāng)加工表面
22、精度較高時(shí),往往要經(jīng)過數(shù)道工序才能達(dá)到要求。對(duì)于右支架的加工要求可知,只有55mm的孔加工表面精度要求比較高,其他表面只需經(jīng)粗加工工序就能保證設(shè)計(jì)要求。因此只需計(jì)算55mm孔的工序尺寸、余量及公差。55mm孔的加工需要經(jīng)過三道工序,并且定位基準(zhǔn)與工序基準(zhǔn)重合。由前知其總加工余量為6mm,其公差等級(jí)為IT8級(jí)。參考臥式銑鏜床的切削用量和加工精度參數(shù),由5-24和表5-25知精鏜時(shí)直徑上切深=0.61.2mm表面粗糙度為Ra6.31.6m,孔徑公差帶為H6H8;半精鏜時(shí),=1.53mm、Ra2512.5m,孔徑公差帶為H8H9;粗鏜時(shí)=58mm、Ra25m,孔徑公差帶為H10H12。按照上述方法,
23、確定55mm孔的工序加工余量、工序尺寸公差及表面粗糙度如下表: 55mm孔加工各工序要求加工表面:55mm孔精鏜半精鏜粗鏜毛坯工序雙邊余量/mm0.51.54工序尺寸及公差/mm550.02491表面粗糙的/m1.66.3258、 確定切削用量和基本時(shí)間 切削用量包含切削速度、進(jìn)給量及背吃刀量三項(xiàng),確定的方法是先確定背吃刀量,進(jìn)給量f,而后確定切削速度v。不同的加工性質(zhì),對(duì)切削加工的要求是不一樣的。因此,在選擇切削用量時(shí),考慮的側(cè)重點(diǎn)也有所不區(qū)別。(一)工序05(粗銑頂面A)切削用量及其基本時(shí)間的確定切削用量本道工序是粗細(xì)端面,已知加工材料為ZG310-570,=570MPa,鑄件無外皮,機(jī)床
24、為XA5032型立式銑床,所選刀具為高速鋼鑲齒套式面銑刀,其參數(shù):直徑d=125mm,孔徑D=40mm,寬L=40mm,齒數(shù)z=14.根據(jù)表5-26確定銑刀角度,選擇前角=20,后角=12,主偏角,螺旋角。已知銑削寬度aw=94mm,銑削背吃刀量=4mm。 確定每齒進(jìn)給量 根據(jù)表5-13知XA5032型立式銑床的主電動(dòng)機(jī)功率為7.5kW,查表5-27知當(dāng)工藝系統(tǒng)剛性中等、鑲齒端銑刀加工鋼料時(shí),每齒進(jìn)給量=0.080.15mm/z。由于本工序背吃刀量和銑削寬度較大,選擇最小的吃進(jìn)給量=0.08mm/z. 選擇銑刀鈍磨標(biāo)準(zhǔn)和耐用度 根據(jù)表5-28,用高速鋼鑲齒端銑刀粗加工鋼料時(shí),選擇銑刀后刀面磨損
25、極限為1.8mm,已知銑刀直徑d=125mm,查表5-29經(jīng)插值的端銑刀的合理耐用度T=150min。 確定切削速度和工作臺(tái)每分鐘進(jìn)給量 根據(jù)表5-30知,高速鋼銑削速度1525m/min, 38.263.7r/min根據(jù)XA5032型立式銑床轉(zhuǎn)速表,選擇n=60r/min=1r/s,則實(shí)際切削速度v:=23.55m/min工作臺(tái)每分鐘進(jìn)給量為:=zn=0.081460=67.2mm/min根據(jù)XA5032型立式銑床工作臺(tái)進(jìn)給量表5-13,選擇標(biāo)準(zhǔn)縱向進(jìn)給量,選取=60mm/min,則實(shí)際的每齒進(jìn)給量為:=0.071mm/z 校驗(yàn)機(jī)床功率根據(jù)表5-31和5-32的計(jì)算公式,銑削時(shí)的功率(kw)
26、和切削力的計(jì)算公式為: (kW) (5-1-2) (N) (5-1-3)式中:所以切削力為:切削時(shí)的功率為:kW=1.31kWXA5032銑床主電動(dòng)機(jī)功率為7.5kW,故所選切削用量合適。最后所確定的切削用量為:。 基本時(shí)間根據(jù)表5-33知,90的端銑刀對(duì)稱銑削的基本時(shí)間為: 其中:L工件銑削部分長(zhǎng)度,單位mm;切入行程長(zhǎng)度,單位mm ,2) 切出行程長(zhǎng)度,單位mm,=13工作臺(tái)每分鐘進(jìn)給量,單位mm/min。已知:=60mm/min,=94mm,=1mm,=0.5(125-+(12)=25mm,+=26mm;所以:=2min。(二)工序15(粗鏜49mm孔及退刀槽356mm)切削用量及基本時(shí)
27、間的確定 本工序?yàn)榇昼M及切退刀槽,已知條件與工序05相同,機(jī)床采用最常用的CA6140臥式車床,工步1采用YT5硬質(zhì)合金刀具,根據(jù)加工條件和工件材料由表5-35、表5-36得刀具參數(shù)為主偏角、前角、刃傾角、刀尖圓弧半徑。選用桿部直徑為20mm得圓形鏜刀。由表5-40知鏜刀的鈍磨標(biāo)準(zhǔn)為1.4mm,鏜刀合理耐用度為T=60min。工步2采用高速鋼內(nèi)孔切槽加工完成。1 確定粗鏜49mm孔的切削用量 確定背吃刀量: 由前述可知粗鏜是雙邊加工余量為6mm,粗鏜后孔直徑為49mm,故單邊余量為3mm,即=3mm。 確定進(jìn)給量: 根據(jù)表5-41,當(dāng)粗鏜鋼料,鏜刀桿直徑為20mm,=3mm,鏜刀伸出長(zhǎng)度為10
28、0mm時(shí),=0.150.25mm/r。按CA6140車床的進(jìn)給量(表5-57),選擇=0.20mm/r。 確定切削速度v : 根據(jù)表5-43的計(jì)算公式確定切削速度 式中,m=0.20。因本例中的加工條件與公式條件不完全相同,故需根據(jù)表5-32對(duì)鏜削速度進(jìn)行修正:根據(jù)刀具耐用度T=60min,得修正系數(shù)=1.0;根據(jù)工件材料MPa,得修正系數(shù);根據(jù)毛坯表面狀態(tài)得修正系數(shù)為=1.0;刀具材料為YT5,的修正系數(shù)=0.65;此處為鏜孔,經(jīng)插值得修正系數(shù)=0.765;主偏角,得修正系數(shù)=1.0。所以m/min=88.1m/min查表5-44,根據(jù)CA6140機(jī)床上的主軸轉(zhuǎn)速n=560r/min,則實(shí)際
29、切削速度為 檢驗(yàn)機(jī)床功率: 由表2-10查得切削力和切削功率計(jì)算公式如下: (N) (5-3-2) (kW) (5-3-3)其中,=2650,=1.0,=0.75,=-0.15,由表5-32得:與刀具耐用度有關(guān)的修正系數(shù)=1.0;與工件材料有關(guān)的修正系數(shù)=0.92;經(jīng)插值得鏜孔相對(duì)于外圓縱車時(shí)的修正系數(shù)=1.04;與主偏角有關(guān)的修正系數(shù)=1.0;與前角有關(guān)的修正系數(shù)=1.04。因此總的修正系數(shù)為=1.00.921.041.01.04=1.0所以,切削力為N=1214.06N切削功率為kW=1.45kW根據(jù)表5-55知:CA6140機(jī)床主軸電動(dòng)機(jī)功率=7.5kW,因,故上述切削用量可用。最后確定
30、的切削用量為:=3mm,=0.2mm/r,=88.1m/min(n=560r/min)。2 確定加工退刀槽的切削用量選用高速鋼切槽刀,采用手動(dòng)進(jìn)給,選擇主軸轉(zhuǎn)速n=40r/min,切削速度為:3 基本時(shí)間由表2-24得鏜孔的基本時(shí)間為 式中,切削加工長(zhǎng)度,單位為mm; 刀具切入長(zhǎng)度,單位為mm,3); 刀具切出長(zhǎng)度,單位為mm,=(35)mm; 單件小批生產(chǎn)時(shí)的試切長(zhǎng)度,單位為mm; 進(jìn)給次數(shù)。已知=9mm,=mm=5.5mm,=4mm,=0,=0.2mm/r,n=560r/min,=1。所以,基本時(shí)間為=0.165min三)工序20(粗鏜55mm孔及倒角C2)切削用量及基本時(shí)間的確定 本工序
31、為粗鏜及倒角C2,機(jī)床采用最常用的CA6140臥式車床,兩個(gè)工步采用YT5硬質(zhì)合金刀具,根據(jù)加工條件和工件材料由表5-35、表5-36得刀具參數(shù)為主偏角、前角、刃傾角、刀尖圓弧半徑。選用桿部直徑為20mm得圓形鏜刀。由表5-40知鏜刀的鈍磨標(biāo)準(zhǔn)為1.4mm,鏜刀合理耐用度為T=60min。1 確定粗鏜55mm孔的切削用量 確定背吃刀量: 由前述可知粗鏜是雙邊加工余量為4mm,粗鏜后孔直徑為53mm,故單邊余量為2mm,即=2mm。 確定進(jìn)給量: 根據(jù)表5-41,當(dāng)粗鏜鋼料,鏜刀桿直徑為20mm,=2mm,鏜刀伸出長(zhǎng)度為100mm時(shí),=0.150.30mm/r。按CA6140車床的進(jìn)給量(表5-
32、42),選擇=0.20mm/r。 確定切削速度v : 根據(jù)表5-43的計(jì)算公式確定切削速度 (5-4-1)式中,m=0.20。因本例中的加工條件與公式條件不完全相同,故需根據(jù)表5-32對(duì)鏜削速度進(jìn)行修正:根據(jù)刀具耐用度T=60min,的修正系數(shù)=1.0;根據(jù)工件材料MPa,得修正系數(shù)=1.18;根據(jù)毛坯表面狀態(tài)得修正系數(shù)為=1.0;刀具材料為YT5,的修正系數(shù)=0.65;此處為鏜孔,經(jīng)插值得修正系數(shù)=0.765;主偏角,得修正系數(shù)=1.0。所以m/min=93.6m/min查表5-44,根據(jù)CA6140機(jī)床上的主軸轉(zhuǎn)速n=560r/min,則實(shí)際切削速度為 檢驗(yàn)機(jī)床功率: 由表2-10查得切削
33、力和切削功率計(jì)算公式如下: (N) (5-4-2) (kW) (5-4-3)其中,=2650,=1.0,=0.75,=-0.15,由表5-32得:與刀具耐用度有關(guān)的修正系數(shù)=1.0;與工件材料有關(guān)的修正系數(shù)=0.92;經(jīng)插值得鏜孔相對(duì)于外圓縱車時(shí)的修正系數(shù)=1.04;與主偏角有關(guān)的修正系數(shù)=1.0;與前角有關(guān)的修正系數(shù)=1.04。因此總的修正系數(shù)為=1.00.921.041.01.04=1.0所以,切削力為N=802.99N切削功率為kW=1.25kW根據(jù)表5-46知:CA6140機(jī)床主軸電動(dòng)機(jī)功率=7.5kW,因,故上述切削用量可用。最后確定的切削用量為:=2mm,=0.2mm/r,=93.
34、2m/min(n=560r/min)。2 確定加工倒角切削用量因?yàn)樵摴ば蛑械牡菇侵饕菫榱搜b配方便,故在實(shí)際生產(chǎn)過程中,加工倒角時(shí)并不需要詳細(xì)的計(jì)算,切削用量與粗鏜55mm孔的相同即可。3 基本時(shí)間由表2-24得鏜孔的基本時(shí)間為 (5-4-4)式中,切削加工長(zhǎng)度,單位為mm; 刀具切入長(zhǎng)度,單位為mm,3); 刀具切出長(zhǎng)度,單位為mm,=(35)mm; 單件小批生產(chǎn)時(shí)的試切長(zhǎng)度,單位為mm; 進(jìn)給次數(shù)。已知=91mm,=mm=4.5mm,=4mm,=0,=0.2mm/r,n=560r/min,=1。所以,基本時(shí)間為=0.89min(四)工序25(半精鏜55mm孔)切削用量及基本時(shí)間的確定 本工
35、序?yàn)榘刖M55mm孔,機(jī)床采用最常用的CA6140臥式車床,采用YT15硬質(zhì)合金刀具,根據(jù)加工條件和工件材料由表5-35、表5-36得刀具參數(shù)為主偏角、前角、刃傾角、刀尖圓弧半徑。選用桿部直徑為20mm得圓形鏜刀。由表5-40知鏜刀的鈍磨標(biāo)準(zhǔn)為1.4mm,鏜刀合理耐用度為T=60min。1 確定半精鏜55mm孔的切削用量 確定背吃刀量: 由前述可知粗鏜是雙邊加工余量為1.5mm,半精鏜后孔直徑為54.5mm,故單邊余量為0.75mm,即=0.75mm。 確定進(jìn)給量: 對(duì)于半精加工,根據(jù)表5-57,按CA6140機(jī)床的進(jìn)給量(表5-42),選擇=0.10mm/r。 確定切削速度v : 根據(jù)表2-
36、8的計(jì)算公式確定切削速度 (5-5-1)式中,m=0.20。因本例中的加工條件與公式條件不完全相同,故需根據(jù)表5-32對(duì)鏜削速度進(jìn)行修正:根據(jù)刀具耐用度T=60min,的修正系數(shù)=1.0;根據(jù)工件材料MPa,得修正系數(shù)=1.18;根據(jù)毛坯表面狀態(tài)得修正系數(shù)為=1.0;刀具材料為YT5,的修正系數(shù)=0.65;此處為鏜孔,經(jīng)插值得修正系數(shù)=0.765;主偏角,得修正系數(shù)=1.0。所以m/min=191.7m/min查表5-44,根據(jù)CA6140機(jī)床上的主軸轉(zhuǎn)速n=900r/min,則實(shí)際切削速度為 檢驗(yàn)機(jī)床功率: 由表2-10查得切削力和切削功率計(jì)算公式如下: (N) (5-5-2) (kW) (
37、5-5-3)其中,=2650,=1.0,=0.75,=-0.15,由表5-32得:與刀具耐用度有關(guān)的修正系數(shù)=1.0;與工件材料有關(guān)的修正系數(shù)=0.92;經(jīng)插值得鏜孔相對(duì)于外圓縱車時(shí)的修正系數(shù)=1.04;與主偏角有關(guān)的修正系數(shù)=1.0;與前角有關(guān)的修正系數(shù)=1.04。因此總的修正系數(shù)為=1.00.921.041.01.04=1.0所以,切削力為N=166N切削功率為kW=0.43kW根據(jù)表5-46知:CA6140機(jī)床主軸電動(dòng)機(jī)功率=7.5kW,因,故上述切削用量可用。最后確定的切削用量為:=0.75mm,=0.1mm/r,=154m/min(n=900r/min)。2 基本時(shí)間由表5-47得鏜
38、孔的基本時(shí)間為 式中,切削加工長(zhǎng)度,單位為mm; 刀具切入長(zhǎng)度,單位為mm,3); 刀具切出長(zhǎng)度,單位為mm,=(35)mm; 單件小批生產(chǎn)時(shí)的試切長(zhǎng)度,單位為mm; 進(jìn)給次數(shù)。已知=91mm,=mm=3.25mm,=4mm,=0,=0.1mm/r,n=900r/min,=1。所以,基本時(shí)間為=1.14min(五)工序45(鉆4M20螺紋底孔18mm)切削用量及基本時(shí)間的確定 本工序?yàn)殂@4個(gè)M20mm孔,所用機(jī)床為Z3025搖臂鉆床。根據(jù)表5-19知選取d=18mm,L=228mm,莫氏圓錐號(hào)為2號(hào)的莫氏錐柄麻花鉆作為刀具。根據(jù)表5-84選擇的鉆頭參數(shù),2=118,=50,。由表5-48知,當(dāng)
39、20mm時(shí),選擇鉆頭刀面磨損極限為0.8mm,耐用度T=45min。1 確定鉆4M20螺紋底孔18mm的切削用量 確定背吃刀量: 鉆孔時(shí),=9mm。 確定進(jìn)給量: 按照加工要求決定進(jìn)給量。鉆頭直徑=18mm,工件材料為鑄鋼且=570MPa時(shí),根據(jù)表5-50,進(jìn)給量取值范圍為0.35-0.43mm/r。由于鉆孔后要用絲錐螺紋,需乘上系數(shù)0.5,又由于鉆孔深度大于3倍直徑,需乘上修正系數(shù)。由于,經(jīng)插值得=0.95。綜上得進(jìn)給量的取值范圍=(0.350.43)0.50.95mm/r=(0.1660.204)mm/r。根據(jù)Z3025機(jī)床標(biāo)準(zhǔn)進(jìn)給量,查表5-51,選取=0.2mm/r。 確定切削速度:
40、根據(jù)表5-52的計(jì)算公式確定切削速度 (m/min) 式中,=0.4,=0.7,m=0.2。因本例的加工條件與該公式應(yīng)用條件不完全相同,故需要對(duì)切削速度進(jìn)行修正。由表5-53得:根據(jù)刀具耐用度T=45min,得修正系數(shù);工件材料=570MPa,得修正系數(shù);鉆孔時(shí)工件經(jīng)過退火熱處理,得修正系數(shù)=0.9;刀具材料為高速鋼,得修正系數(shù)=1.0;鉆頭為標(biāo)準(zhǔn)刃磨形狀,得修正系數(shù)=0.87;鉆孔深度,得修正系數(shù)。所以=1.01.160.91.00.870.85=0.770.77=15.51m/min=274.4r/min根據(jù)Z3025機(jī)床標(biāo)準(zhǔn)主軸轉(zhuǎn)速,由表5-54選取n=250r/min,實(shí)際轉(zhuǎn)速為m/m
41、in 校驗(yàn)機(jī)床功率: 由表5-55知,查得轉(zhuǎn)矩和切削功率計(jì)算公式如下: =(Nm) (5-9-2) (5-9-3)式中:=0.305,=2.0,=0.8,,由表5-56得:與加工材料有關(guān)的修正系數(shù)=0.88;與刃磨形狀有關(guān)的修正系數(shù)=1.0;與刀具磨鈍有關(guān)的修正系數(shù)=0.87。因此總的修正系數(shù)為:=0.881.00.87=0.77。所以擴(kuò)孔時(shí)轉(zhuǎn)矩為Nm=21Nm切削功率為kW由表5-14知,Z3025機(jī)床主軸最大轉(zhuǎn)速=196.2Nm。主電動(dòng)機(jī)功率=2.2kW。由于,故選擇的切削用量可用。最后所確定的切削用量為=9mm,=0.2mm/r,=14.1m/min(n=250r/min)。 基本時(shí)間由
42、表5-57得擴(kuò)孔的基本時(shí)間 式中,工件切削部分長(zhǎng)度,單位為mm; 刀具切入長(zhǎng)度,單位為mm,+3; 刀具超出長(zhǎng)度,單位為mm,=(24)mm;已知:=70mm,=8.4mm,=3mm,=0.2mm/r,n=250r/min。所以,加工4個(gè)孔所用的基本時(shí)間為六)工序50(精鏜55mm孔及倒角C2)切削用量及基本時(shí)間的確定 本工序?yàn)榫M及倒角C2,機(jī)床采用最常用的CA6140臥式車床,兩個(gè)工步采用YT30硬質(zhì)合金刀具,根據(jù)加工條件和工件材料由表5-35、表5-36得刀具參數(shù)為主偏角、前角、刃傾角、刀尖圓弧半徑。選用桿部直徑為20mm得圓形鏜刀。由表5-40知鏜刀的鈍磨標(biāo)準(zhǔn)為0.6mm,鏜刀合理耐用
43、度為T=60min。1 確定精鏜55mm孔的切削用量 確定背吃刀量: 由前述可知粗鏜是雙邊加工余量為0.5mm,粗鏜后孔直徑為55mm,故單邊余量為0.25mm,即=0.25mm。 確定進(jìn)給量: 對(duì)于精加工,根據(jù)表5-42,按照CA6140車床的進(jìn)給量,選擇=0.08mm/r。 確定切削速度v : 根據(jù)表5-43的計(jì)算公式確定切削速度 (5-10-1)式中,m=0.20。因本例中的加工條件與公式條件不完全相同,故需根據(jù)表5-32對(duì)鏜削速度進(jìn)行修正:根據(jù)刀具耐用度T=60min,的修正系數(shù)=1.0;根據(jù)工件材料MPa,得修正系數(shù)=1.18;根據(jù)毛坯表面狀態(tài)得修正系數(shù)為=1.0;刀具材料為YT30
44、,得修正系數(shù)=1.4;此處為鏜孔,經(jīng)插值得修正系數(shù)=0.765;主偏角,得修正系數(shù)=1.0。所以m/min=330.8m/min查表5-44,根據(jù)CA6140機(jī)床上的主軸轉(zhuǎn)速n=1400r/min,則實(shí)際切削速度為 檢驗(yàn)機(jī)床功率: 由表5-45查得切削力和切削功率計(jì)算公式如下: (N) (5-10-2) (kW) (5-10-3)其中,=2650,=1.0,=0.75,=-0.15,由表5-32得:與刀具耐用度有關(guān)的修正系數(shù)=1.0;與工件材料有關(guān)的修正系數(shù)=0.92;經(jīng)插值得鏜孔相對(duì)于外圓縱車時(shí)的修正系數(shù)=1.04;與主偏角有關(guān)的修正系數(shù)=1.0;與前角有關(guān)的修正系數(shù)=1.04。因此總的修正
45、系數(shù)為=1.00.921.041.01.04=1.0所以,切削力為N=43.75N切削功率為kW=0.18kW根據(jù)表5-46知:CA6140機(jī)床主軸電動(dòng)機(jī)功率=7.5kW,因,故上述切削用量可用。最后確定的切削用量為:=0.25mm,=0.08mm/r,=241.78m/min(n=1400r/min)。2 確定加工倒角切削用量因?yàn)樵摴ば蛑械牡菇侵饕菫榱搜b配方便,故在實(shí)際生產(chǎn)過程中,加工倒角時(shí)并不需要詳細(xì)的計(jì)算,切削用量與精鏜55mm孔的相同即可。3 基本時(shí)間由表5-47得鏜孔的基本時(shí)間為 (5-10-4)式中,切削加工長(zhǎng)度,單位為mm; 刀具切入長(zhǎng)度,單位為mm,3); 刀具切出長(zhǎng)度,單位
46、為mm,=(35)mm; 單件小批生產(chǎn)時(shí)的試切長(zhǎng)度,單位為mm; 進(jìn)給次數(shù)。已知=91mm,=mm=2.75mm,=4mm,=0,=0.08mm/r,n=1400r/min,=1。所以,基本時(shí)間為=0.87min(七)工序55(銑開工序)的切削用量及其基本時(shí)間的確定 本工序?qū)⒅Ъ芰慵婇_成上蓋和支架座兩個(gè)部分。沿55mm孔中心線銑斷,分兩次安裝。第一次先銑開一側(cè)。采用的機(jī)床為常見的XA6132臥式銑床,由表5-13知其主電動(dòng)機(jī)功率為7.5kW。刀具為=160mm,D=32mm,L=6mm,z=48mm的鋸片銑刀。已知銑削寬度=43mm,背吃刀量=5mm。1 切削用量 選擇銑刀鈍磨標(biāo)準(zhǔn)和耐用度:
47、 查表5-28,選擇后刀面磨損量極限為0.2mm,由表5-29經(jīng)插值得銑削耐用度T=186min。 確定每齒進(jìn)給量: 根據(jù)表5-74知XA6132型立式銑床的主電動(dòng)機(jī)功率為7.5kW,已知當(dāng)工藝系統(tǒng)剛性中等、切斷銑刀加工鋼料時(shí),每齒進(jìn)給量=0.020.01mm/z。由于本工序背吃刀量和銑削寬度較大,選擇最小的吃進(jìn)給量=0.016mm/z 確定切削速度v和工作臺(tái)每分鐘進(jìn)給量及每齒進(jìn)給量: 由表5-30知,高速鋼銑刀銑削鑄鋼的切削速度v為1525m/min則所需銑床主軸轉(zhuǎn)速:29.8549.67r/min由于本工序銑削深度和寬度較大,切斷工況惡劣,故選擇最小的主軸轉(zhuǎn)速縱向進(jìn)給量。根據(jù)XA6132臥
48、式銑床的標(biāo)準(zhǔn)株洲轉(zhuǎn)速和標(biāo)準(zhǔn)縱向進(jìn)給量,(見表5-13)選取主軸轉(zhuǎn)速n=30r/min,工作臺(tái)縱向進(jìn)給速度vf=23.5mm/min。則實(shí)際切削速度為:=15.1m/min工作臺(tái)每齒進(jìn)給量為:= 校驗(yàn)機(jī)床功率: 根據(jù)表2-18的計(jì)算公式,銑削時(shí)的功率(kw)和切削力的計(jì)算公式為: (kW) (N) 式中:與工件材料有關(guān)的修正系數(shù)為0.92,因此=0.92,所以切削力為切削時(shí)的功率為:kW=0.59kWXA6132銑床主電動(dòng)機(jī)功率為7.5kW,故所選切削用量合適。最后所確定的切削用量為: 。 基本時(shí)間 其中:L工件銑削部分長(zhǎng)度,單位mm;切入行程長(zhǎng)度,單位mm ,; 切出行程長(zhǎng)度,單位mm,=13
49、 工作臺(tái)每分鐘進(jìn)給量,單位mm/min。已知:=23.5mm/min,=100mm,=0.5160=80mm,=1mm,+=8所以:=15.4min。(八)工序65(倒角底孔并攻支架體螺紋4M202)切削用量及基本時(shí)間的確定 本工序?yàn)榈菇堑卓撞⒐ブЪ荏w螺紋4M202,所用機(jī)床為Z3025搖臂鉆床。根據(jù)表5-58知工步1采用90錐柄錐面锪鉆加工,d=40mm,L=150mm,莫氏圓錐號(hào)為3號(hào)。由表5-49知,刀具耐用度為T=50min。工步2采用M202細(xì)柄機(jī)用高速鋼絲錐,由表5-21知=37mm,L=112mm,由表5-59知工件材料為中碳鋼時(shí),取絲錐前角,后角。刀具耐用度T=90min。 確
50、定倒角的切削用量 確定進(jìn)給量: 按照加工要求決定進(jìn)給量。根據(jù)表5-60,進(jìn)給量取值范圍為0.080.15mm/r。根據(jù)Z3025機(jī)床標(biāo)準(zhǔn)進(jìn)給量,查表5-63,選取=0.12mm/r。 確定切削速度: 根據(jù)表5-60知锪鉆加工的切削速度為2326m/min,則所需銑床主軸轉(zhuǎn)速范圍為183.1207r/min根據(jù)Z3025機(jī)床標(biāo)準(zhǔn)主軸轉(zhuǎn)速,由表5-54選取n=200r/min,實(shí)際轉(zhuǎn)速為m/min最后所確定的切削用量為:=0.12mm/r;m/min(n=200r/min)。2 確定攻螺紋的切削用量 確定背吃刀量: =1mm。 確定進(jìn)給量: 等于工件螺紋的螺距,即=2mm/r。 確定切削速度: 根
51、據(jù)表5-61的計(jì)算公式確定切削速度 (m/min) 式中,=1.2,=0.5,m=0.9。工件材料=570MPa,得修正系數(shù);刀具材料修正系數(shù)=1.0;螺紋公差等級(jí)修正系數(shù)=1.0;絲錐芯部直徑=(0.40.5),其中d為絲錐大徑,取=0.5d=0.520=10。所以:=1.01.01.0=11.0=12.7m/min=202.2r/min根據(jù)Z3025機(jī)床標(biāo)準(zhǔn)主軸轉(zhuǎn)速,由表5-62選取n=200r/min,實(shí)際轉(zhuǎn)速為m/min 校驗(yàn)機(jī)床功率: 由表5-61知,查得轉(zhuǎn)矩和切削功率計(jì)算公式如下: =(Nm) 式中:=0.264,=1.4,=1.5,=1.0,則轉(zhuǎn)矩為: Nm=18.76Nm切削功
52、率為kW由表5-14知,Z3025機(jī)床主軸最大轉(zhuǎn)速=196.2Nm。主電動(dòng)機(jī)功率=2.2kW。由于,故選擇的切削用量可用。最后所確定的切削用量為=1mm,=2mm/r,=12.56m/min(n=200r/min)。3 基本時(shí)間 工步1的基本時(shí)間: 根據(jù)表5-57知锪倒角的基本時(shí)間為:式中,工件切削部分長(zhǎng)度,單位為mm; 切入量,單位為mm,=(1.53)mm已知=2mm,取為2mm。所以,加工四個(gè)孔所用的基本時(shí)間為min=0.67min 工步2的基本時(shí)間: 選取絲錐退出的轉(zhuǎn)速比攻螺紋時(shí)的轉(zhuǎn)速高一等級(jí),根據(jù)表2-24知=250r/min,則根據(jù)表5-62,機(jī)用絲錐攻螺紋的機(jī)動(dòng)時(shí)間計(jì)算公式為:
53、式中, =27mm,P=2mm,n=200r/min,=250r/min,為工件每轉(zhuǎn)進(jìn)給量,等于工件螺紋的螺距,即=2mm/r,=(13)P=2P=4mm,=0。則:又因再次道工序中要攻制4個(gè)相同的螺紋孔,所以4次攻螺紋所用的基本時(shí)間為:=0.56min(九)工序70:去毛刺、清洗、檢驗(yàn)。第二部分專用夾具的設(shè)計(jì)一、 接受設(shè)計(jì)任務(wù)、明確加工要求本次專用機(jī)床夾具設(shè)計(jì)任務(wù)是設(shè)計(jì)用于加工東方紅75推土機(jī)鏟臂右支架二個(gè)43.5mm孔的鉆模,具體設(shè)計(jì)內(nèi)容和要求應(yīng)以機(jī)械制造工藝學(xué)課程設(shè)計(jì)任務(wù)書和右鏟臂支架機(jī)械加工工藝規(guī)程為依據(jù)。有關(guān)零件功用、工作條件方面的內(nèi)容可參照零件圖樣和機(jī)械工藝規(guī)程制訂部分。由零件圖樣
54、和課程設(shè)計(jì)任務(wù)書中能得到的本工序加工要求如下: 2個(gè)mm尺寸公差等級(jí)要求為IT13級(jí)。 2個(gè)mm孔表面粗糙度要求為Ra12.5m。 2個(gè)mm孔深均為62mm。 2個(gè)mm軸線對(duì)55mm孔軸線的垂直度公差為0.2/100。 2個(gè)mm孔軸線夾角為4610,兩孔軸線關(guān)于主視圖中的豎直中心線對(duì)稱且夾角頂點(diǎn)在55mm孔的軸線上。 零件毛坯材料為ZG310570。 產(chǎn)品生產(chǎn)綱領(lǐng):4905件/年。擴(kuò)2個(gè)mm孔在整個(gè)機(jī)加工工藝規(guī)程中為第六道工序(工序30),加工之前55mm孔已進(jìn)行半精加工,其加工后尺寸為54.5H9()mm,表面粗糙度為Ra12.5m;A面及B和C面以加工完畢,表面粗糙度為Ra12.5m。A、
55、B和C面與55mm孔雖在不同工序中加工,但位置精度較高。本零件毛坯為砂型機(jī)器造型,加工前退火處理,硬度為156217HBW。鑄造分型面在主視圖投影的最大輪廓線上,鑄件公差等級(jí)為CT9級(jí)。按毛坯的供應(yīng)狀態(tài),分型面處毛刺又已經(jīng)磨平,零件外部未加工表面基本平整光滑,被加工孔處單邊加工余量為3mm。二、 確定定位方案、選擇定位元件 確定定位方案在鉆模的設(shè)計(jì)中,工件的定位方案與定位基準(zhǔn)面的選擇一般應(yīng)與該工件的機(jī)械加工工藝規(guī)程一致。若工藝規(guī)程中的定位方案與定位基準(zhǔn)面的選擇確有問題時(shí),可重新進(jìn)行考慮和確定。由零件圖樣和該零件的機(jī)械加工工藝規(guī)程可知工件上2個(gè)43.5mm孔與 55mm孔軸線有垂直度的要求,且2
56、個(gè)43.5孔軸線的交點(diǎn)與55mm孔軸線重合,這表明2個(gè)43.5mm孔的工序基準(zhǔn)為55mm孔,在定位基準(zhǔn)面與定位方案選擇上應(yīng)該以55mm孔為定位基準(zhǔn),以避免由于基準(zhǔn)不重合帶來的加工誤差。有零件的加工要求可知,用“調(diào)整法”加工2個(gè)43.5mm孔時(shí)必須限制6個(gè)自由度,若選55mm孔為第一定位基準(zhǔn)只能限制4個(gè)自由度,還必須另選定位基準(zhǔn)面來滿足定位要求。由有前面分析可知,還可利用的表面有已加工好的A、B平面。若選任一平面為為第二定位基準(zhǔn)面,這時(shí)限制3個(gè)自由度,共限制了7個(gè)自由度,其中兩個(gè)自由度被重復(fù)限制。此外,長(zhǎng)心軸和平面的定位方式中,還有一個(gè)繞55mm軸線轉(zhuǎn)動(dòng)的自由度未被限制,故應(yīng)以2個(gè)43.5mm孔
57、之一的外援作為第三定位基準(zhǔn)限制其轉(zhuǎn)動(dòng)自由度。為了解決過定位的問題,可以采取兩種途徑: 減少定位心軸的長(zhǎng)度,改長(zhǎng)定位心軸為短定位心軸,55mm孔由第一定位基準(zhǔn)變?yōu)榈诙ㄎ换鶞?zhǔn),所限制的自由度數(shù)由4個(gè)變?yōu)?個(gè),第一定位基準(zhǔn)則為B、C構(gòu)成的平面; 提高工件上55mm孔與B、C構(gòu)成平面的垂直度要求,同時(shí)提高夾具上定位心軸與其端面的垂直度要求。這樣,此種定位方式表面上看是過定位,但實(shí)際上并不會(huì)出現(xiàn)定位所造成的一批工件定位不統(tǒng)一、裝卡困難、工件和定位元件發(fā)生變形等惡果。經(jīng)綜合分析比較,最終選擇B、C構(gòu)成的平面作為第一定位基準(zhǔn),限制3個(gè)自由度。55mm孔作為第二定位基準(zhǔn),限制2個(gè)自由度。2個(gè)43.5mm孔之一的外緣作為第三定位基準(zhǔn),限制1個(gè)自由度。結(jié)果與右支架機(jī)械加工工藝規(guī)程中的定位方案一致。1 選擇定位元件工件的定位是通過定位基準(zhǔn)面與定位元件接觸來實(shí)現(xiàn)的,故定位元件的選取應(yīng)與定位方案和工件定位表面相適應(yīng)。因此對(duì)于此工件的定位元件選擇為: 第一定位基準(zhǔn):55mm短心軸臺(tái)肩與分度盤所構(gòu)成的大平面。 第二定位基準(zhǔn):55mm短心軸。 第三定位基準(zhǔn):擋銷。三、確定夾緊方案、設(shè)計(jì)夾緊機(jī)構(gòu)根據(jù)工件的形狀特點(diǎn)和定位方案,可采取以下兩種夾緊方案:一種為手動(dòng)螺
- 溫馨提示:
1: 本站所有資源如無特殊說明,都需要本地電腦安裝OFFICE2007和PDF閱讀器。圖紙軟件為CAD,CAXA,PROE,UG,SolidWorks等.壓縮文件請(qǐng)下載最新的WinRAR軟件解壓。
2: 本站的文檔不包含任何第三方提供的附件圖紙等,如果需要附件,請(qǐng)聯(lián)系上傳者。文件的所有權(quán)益歸上傳用戶所有。
3.本站RAR壓縮包中若帶圖紙,網(wǎng)頁(yè)內(nèi)容里面會(huì)有圖紙預(yù)覽,若沒有圖紙預(yù)覽就沒有圖紙。
4. 未經(jīng)權(quán)益所有人同意不得將文件中的內(nèi)容挪作商業(yè)或盈利用途。
5. 裝配圖網(wǎng)僅提供信息存儲(chǔ)空間,僅對(duì)用戶上傳內(nèi)容的表現(xiàn)方式做保護(hù)處理,對(duì)用戶上傳分享的文檔內(nèi)容本身不做任何修改或編輯,并不能對(duì)任何下載內(nèi)容負(fù)責(zé)。
6. 下載文件中如有侵權(quán)或不適當(dāng)內(nèi)容,請(qǐng)與我們聯(lián)系,我們立即糾正。
7. 本站不保證下載資源的準(zhǔn)確性、安全性和完整性, 同時(shí)也不承擔(dān)用戶因使用這些下載資源對(duì)自己和他人造成任何形式的傷害或損失。
最新文檔
- 建筑施工重大危險(xiǎn)源安全管理制度
- 安全培訓(xùn)資料:典型建筑火災(zāi)的防治基本原則與救援技術(shù)
- 企業(yè)雙重預(yù)防體系應(yīng)知應(yīng)會(huì)知識(shí)問答
- 8 各種煤礦安全考試試題
- 9 危險(xiǎn)化學(xué)品經(jīng)營(yíng)單位安全生產(chǎn)管理人員模擬考試題庫(kù)試卷附答案
- 加壓過濾機(jī)司機(jī)技術(shù)操作規(guī)程
- 樹脂砂混砂工藝知識(shí)總結(jié)
- XXXXX現(xiàn)場(chǎng)安全應(yīng)急處置預(yù)案
- 某公司消防安全檢查制度總結(jié)
- 1 煤礦安全檢查工(中級(jí))職業(yè)技能理論知識(shí)考核試題含答案
- 4.燃?xì)獍踩a(chǎn)企業(yè)主要負(fù)責(zé)人模擬考試題庫(kù)試卷含答案
- 工段(班組)級(jí)安全檢查表
- D 氯化工藝作業(yè)模擬考試題庫(kù)試卷含答案-4
- 建筑起重司索信號(hào)工安全操作要點(diǎn)
- 實(shí)驗(yàn)室計(jì)量常見的30個(gè)問問答題含解析
相關(guān)資源
更多