專題講座資料(2021-2022年)工業(yè)化學(xué)復(fù)習(xí)題2全解
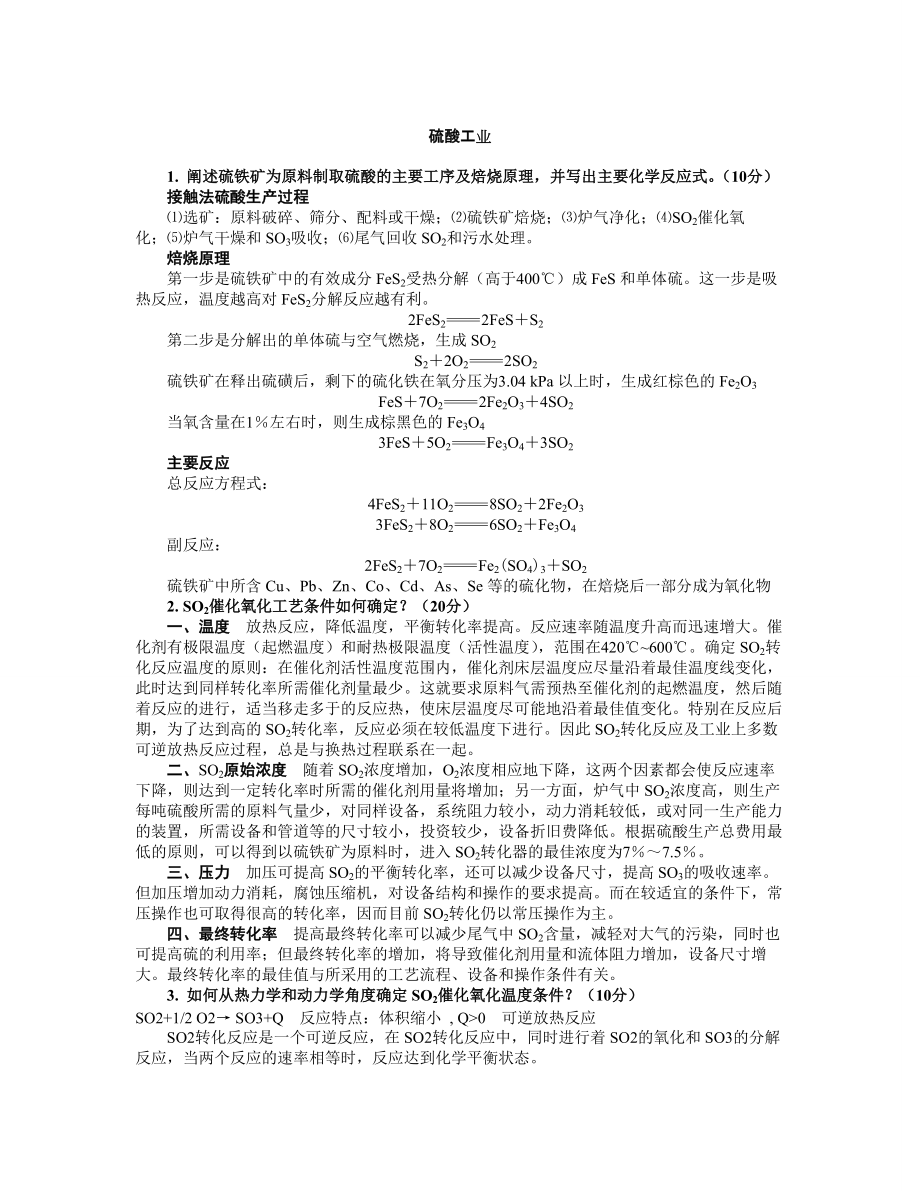


《專題講座資料(2021-2022年)工業(yè)化學(xué)復(fù)習(xí)題2全解》由會(huì)員分享,可在線閱讀,更多相關(guān)《專題講座資料(2021-2022年)工業(yè)化學(xué)復(fù)習(xí)題2全解(8頁珍藏版)》請?jiān)谘b配圖網(wǎng)上搜索。
1、硫酸工業(yè) 1. 闡述硫鐵礦為原料制取硫酸的主要工序及焙燒原理,并寫出主要化學(xué)反應(yīng)式。(10分) 接觸法硫酸生產(chǎn)過程 ⑴選礦:原料破碎、篩分、配料或干燥;⑵硫鐵礦焙燒;⑶爐氣凈化;⑷SO2催化氧化;⑸爐氣干燥和SO3吸收;⑹尾氣回收SO2和污水處理。 焙燒原理 第一步是硫鐵礦中的有效成分FeS2受熱分解(高于400℃)成FeS和單體硫。這一步是吸熱反應(yīng),溫度越高對FeS2分解反應(yīng)越有利。 2FeS2=2FeS+S2 第二步是分解出的單體硫與空氣燃燒,生成SO2 S2+2O2=2SO2 硫鐵礦在釋出硫磺后,剩下的硫化鐵在氧分壓為3.04 kPa以上時(shí),生成紅棕色的Fe2O3 F
2、eS+7O2=2Fe2O3+4SO2 當(dāng)氧含量在1%左右時(shí),則生成棕黑色的Fe3O4 3FeS+5O2=Fe3O4+3SO2 主要反應(yīng) 總反應(yīng)方程式: 4FeS2+11O2=8SO2+2Fe2O3 3FeS2+8O2=6SO2+Fe3O4 副反應(yīng): 2FeS2+7O2=Fe2(SO4)3+SO2 硫鐵礦中所含Cu、Pb、Zn、Co、Cd、As、Se等的硫化物,在焙燒后一部分成為氧化物 2. SO2催化氧化工藝條件如何確定?(20分) 一、溫度 放熱反應(yīng),降低溫度,平衡轉(zhuǎn)化率提高。反應(yīng)速率隨溫度升高而迅速增大。催化劑有極限溫度(起燃溫度)和耐熱極限溫度(活性溫度),范圍在
3、420℃~600℃。確定SO2轉(zhuǎn)化反應(yīng)溫度的原則:在催化劑活性溫度范圍內(nèi),催化劑床層溫度應(yīng)盡量沿著最佳溫度線變化,此時(shí)達(dá)到同樣轉(zhuǎn)化率所需催化劑量最少。這就要求原料氣需預(yù)熱至催化劑的起燃溫度,然后隨著反應(yīng)的進(jìn)行,適當(dāng)移走多于的反應(yīng)熱,使床層溫度盡可能地沿著最佳值變化。特別在反應(yīng)后期,為了達(dá)到高的SO2轉(zhuǎn)化率,反應(yīng)必須在較低溫度下進(jìn)行。因此SO2轉(zhuǎn)化反應(yīng)及工業(yè)上多數(shù)可逆放熱反應(yīng)過程,總是與換熱過程聯(lián)系在一起。 二、SO2原始濃度 隨著SO2濃度增加,O2濃度相應(yīng)地下降,這兩個(gè)因素都會(huì)使反應(yīng)速率下降,則達(dá)到一定轉(zhuǎn)化率時(shí)所需的催化劑用量將增加;另一方面,爐氣中SO2濃度高,則生產(chǎn)每噸硫酸所需的原料
4、氣量少,對同樣設(shè)備,系統(tǒng)阻力較小,動(dòng)力消耗較低,或?qū)ν簧a(chǎn)能力的裝置,所需設(shè)備和管道等的尺寸較小,投資較少,設(shè)備折舊費(fèi)降低。根據(jù)硫酸生產(chǎn)總費(fèi)用最低的原則,可以得到以硫鐵礦為原料時(shí),進(jìn)入SO2轉(zhuǎn)化器的最佳濃度為7%~7.5%。 三、壓力 加壓可提高SO2的平衡轉(zhuǎn)化率,還可以減少設(shè)備尺寸,提高SO3的吸收速率。但加壓增加動(dòng)力消耗,腐蝕壓縮機(jī),對設(shè)備結(jié)構(gòu)和操作的要求提高。而在較適宜的條件下,常壓操作也可取得很高的轉(zhuǎn)化率,因而目前SO2轉(zhuǎn)化仍以常壓操作為主。 四、最終轉(zhuǎn)化率 提高最終轉(zhuǎn)化率可以減少尾氣中SO2含量,減輕對大氣的污染,同時(shí)也可提高硫的利用率;但最終轉(zhuǎn)化率的增加,將導(dǎo)致催化劑用量
5、和流體阻力增加,設(shè)備尺寸增大。最終轉(zhuǎn)化率的最佳值與所采用的工藝流程、設(shè)備和操作條件有關(guān)。 3. 如何從熱力學(xué)和動(dòng)力學(xué)角度確定SO2催化氧化溫度條件?(10分) SO2+1/2 O2→ SO3+Q 反應(yīng)特點(diǎn):體積縮小 , Q>0 可逆放熱反應(yīng) SO2轉(zhuǎn)化反應(yīng)是一個(gè)可逆反應(yīng),在SO2轉(zhuǎn)化反應(yīng)中,同時(shí)進(jìn)行著SO2的氧化和SO3的分解反應(yīng),當(dāng)兩個(gè)反應(yīng)的速率相等時(shí),反應(yīng)達(dá)到化學(xué)平衡狀態(tài)。 SO2轉(zhuǎn)化反應(yīng)是一個(gè)放熱反應(yīng),降低反應(yīng)溫度會(huì)使平衡轉(zhuǎn)化率提高。 反應(yīng)速率隨溫度的升高而迅速增大;但催化劑有起燃溫度,為了保證催化劑的正常使用,應(yīng)該選擇合適的溫度; 在選擇溫度指標(biāo)時(shí),不但要考慮有較高的轉(zhuǎn)
6、化率,還要考慮有較高的反應(yīng)速率。在工業(yè)生產(chǎn)中,可通過分段轉(zhuǎn)化,控制不同的轉(zhuǎn)化溫度來實(shí)現(xiàn)較高的轉(zhuǎn)化率和較快的反應(yīng)速率。反應(yīng)初期宜使氣體在較高的溫度下轉(zhuǎn)化;反應(yīng)的后期,宜使氣體在較低的溫度下轉(zhuǎn)化。 4. 在制取硫酸過程中,常易形成酸霧,試解釋酸霧形成的原因,以及酸霧怎樣清除之。(15分) 酸霧的形成 在爐氣濕法凈化過程中,由于爐氣被洗滌冷卻,大量的水蒸氣進(jìn)入氣相,于是爐氣中的SO3(g)在氣相中發(fā)生反應(yīng),生成了硫酸蒸氣 SO3(g)+H2O(g)=H2SO4(g) 當(dāng)氣相中硫酸蒸氣壓大于洗滌液液面上的飽和蒸氣壓時(shí),硫酸蒸氣就會(huì)冷凝。硫酸蒸氣在氣相中快速冷凝時(shí)就會(huì)形成酸霧。爐氣在洗滌時(shí),冷
7、卻速度是很快的,因而必然會(huì)生成酸霧液滴。如果存在凝結(jié)中心(如雜質(zhì)微粒),則生成酸霧粒子就大。所以,伴隨著爐氣的洗滌、降溫過程,礦塵、砷、硒和氟等雜質(zhì)不斷地從氣相中被除去,同時(shí)產(chǎn)生了酸霧。氣相中殘余的細(xì)小塵粒和砷、硒氧化物懸浮微粒亦成為酸霧的冷凝中心。初形成酸霧霧粒較大,由于氣體中懸浮有各種氣溶膠粒子,硫酸蒸汽就在它們表面發(fā)生冷凝形成直徑較大霧粒。 用特殊方法清除 從分離的角度看,霧不能用普通方法除掉,這是因?yàn)棰偶?xì)小的微粒(滴)傾向于跟隨流體的流線運(yùn)動(dòng),難以通過撞擊方式捕捉,使之與氣體分離;⑵霧粒直徑比分子直徑大得多,故不能通過擴(kuò)散的方式使之進(jìn)入液相,即不能被體吸收。因而酸霧必須用特殊的方法
8、清除。 酸霧的清除 在濕法凈化中,當(dāng)爐氣溫度快速降至100 ℃以下時(shí),爐氣中的硫酸蒸氣幾乎全部變成酸霧。酸霧中較大的粒子(大于2μm)由電除霧器、文氏管、沖擋式洗滌器等裝置可除去,其中電除霧器最為可靠。 對于粒徑小于2 μm的霧粒,提出了對爐氣增濕,使?fàn)t氣中較小的酸霧液滴長大后再清除的方法,即先增大霧粒的直徑,再用相應(yīng)的設(shè)備除之。 以上討論的只是消極的方法,更積極的方法是控制爐氣中SO3含量,減少“原生酸霧”量。 5. 闡述制取硫酸中,煙氣凈化的目的及凈化的原則。 爐氣組成:N2、O2、SO2、As2O3、SeO2、HF、SO3、H2O及礦塵。其中:As2O3、SeO2、HF、SO
9、3、H2O、礦塵必須除去。 目的:爐氣含塵若不除凈,進(jìn)入后制酸系統(tǒng),則會(huì)堵塞設(shè)備和管道,且使催化劑失活或中毒 爐氣的凈化原則 爐氣的雜質(zhì)主要以氣態(tài)、液態(tài)、固態(tài)三種形態(tài)同時(shí)存在,顆粒大小,密度輕重不同(1~1000μm)。 a懸浮微粒,分布很大,大小相差很大,應(yīng)先大后小,先易后難進(jìn)行分級處理 b懸浮顆粒氣固液三態(tài)共存,質(zhì)量相差很大。先重后輕即先固、液,后氣(汽)體 c不同大小的粒子,選擇配套有效的分離設(shè)備。 6. 硫鐵礦焙燒爐中的“沸騰”指的是什么反應(yīng)狀態(tài)?對固體顆粒有什么要求?為什么? 流態(tài)化焙燒。入爐礦粒較細(xì),比表面積大,能與空氣充分接觸,有利于氧的擴(kuò)散,反應(yīng)速
10、度快;硫的燒出率高,礦渣殘硫量低;燃燒速度快,過量空氣少,爐氣中SO2 濃度較高。 7. 爐氣凈化流程的“文-泡-電”和“文-泡-文”水洗凈化流程?評價(jià)其優(yōu)缺點(diǎn)。 1)旋風(fēng)除塵器 ?“文氏管?泡沫洗滌塔?電除霧器” ?濃硫酸干燥塔; 凈化程度高,電除霧器投資較大 2)旋風(fēng)除塵器?“第一文氏管?泡沫洗滌塔?第二文氏管” ?旋風(fēng)除沫器?濃硫酸干燥塔 凈化程度稍低,但投資較少。 8. 指出下表的變化規(guī)律并根據(jù)SO2氧化反應(yīng)熱化學(xué)方程式解釋之。 溫度,℃ 各壓力下的平衡轉(zhuǎn)化率xe ,% 0.1MPa 0.51MPa 1.01MPa
11、 10.1MPa 400 99.2 99.6 99.7 99.9 450 97.5 98.9 99.2 99.7 500 93.5 90.9 97.8 99.3 550 85.6 92.8 94.8 98.3 600 73.7 85.8 89.4 96.3 9. 什么是催化劑的“活性溫度范圍”。 反應(yīng)溫度必須在催化劑的“起燃溫度”(下限)和“耐熱極限溫度”(上限)范圍之內(nèi),這一溫度范圍稱為“活性溫度范圍”。 10. 什么是“最適宜溫度線”?在確定工藝參數(shù)時(shí)有何意義? 瞬時(shí)反應(yīng)速度最大時(shí)的溫度-轉(zhuǎn)化率關(guān)系曲線,稱為“最適宜溫度
12、線”。 最適宜溫度線的重要意義在于:假如催化劑床層中的溫度能隨著轉(zhuǎn)化率的提高而按照最適宜溫度線變化的話,則此時(shí)達(dá)到同樣轉(zhuǎn)化率所需要的催化劑量最少。 11. 解釋下圖。 (1)溫度越低轉(zhuǎn)化率越大;(2)溫度越低瞬時(shí)反應(yīng)速度越低;(3)不同的轉(zhuǎn)化率都存在溫度與反應(yīng)速率的最大極值點(diǎn)。 確定生產(chǎn)工藝時(shí)要綜合考慮轉(zhuǎn)化率和反應(yīng)速度使單位時(shí)間內(nèi)的產(chǎn)量最大化,圖中C-C線與B-B線包含的范圍表示合理范圍,在A-A線是不同產(chǎn)率時(shí)反應(yīng)速率極值點(diǎn)的連線,體現(xiàn)溫度-反應(yīng)速率-產(chǎn)率之間的優(yōu)化結(jié)果。 合成氨工業(yè)與尿素生產(chǎn) 1. 試簡述溫度、壓力及情性氣體含量對氨合成反應(yīng)中平衡氨含量及工藝條件的影響?(
13、12分) 氨合成是物質(zhì)的量減小的放熱可逆反應(yīng)。 N2+H2=NH3;=-46.22 kJ·mol-1 化學(xué)平衡常數(shù)Kp可表示為Kp= 溫度越高,平衡常數(shù)越小。提高壓力,Kp值有所增加。顯然,提高壓力、降低溫度有利于氨的生成。 對氨合成反應(yīng)中工藝條件的影響 (1)壓力 從化學(xué)平衡和化學(xué)反應(yīng)速率的角度看,提高操作壓力是有利的。合成裝置的生產(chǎn)能力隨壓力提高而增加,而且壓力高,氨分離流程可以簡化。但是,壓力高時(shí)對設(shè)備材質(zhì)、加工制造的要求均高。同時(shí),高壓下反應(yīng)溫度一般較高,催化劑使用壽命較短。生產(chǎn)上選擇操作壓力的主要依據(jù)是能量消耗以及包括能量消耗、原料費(fèi)用、設(shè)備投資在內(nèi)的所謂綜合費(fèi)用。根據(jù)
14、實(shí)際情況,我國中小型氨廠大多采用20 MPa~32 MPa。 (2)溫度 氨合成反應(yīng)溫度一般控制在350 ℃~550 ℃。將氣體先預(yù)熱到高于催化劑的活性溫度下限后,送入催化劑床層,在絕熱條件下進(jìn)行反應(yīng),隨著反應(yīng)進(jìn)行,溫度逐漸升高,當(dāng)接近最適溫度后,再采取冷卻措施,使反應(yīng)溫度盡量接近于最適宜溫度曲線。 (3)進(jìn)口氣體組成 惰性氣體(CH4和Ar)由新鮮氣帶入,由于不參加反應(yīng)而在氨合成系統(tǒng)中積累。惰性氣體的存在,無論從熱力學(xué)還是動(dòng)力學(xué)上考慮都使不利的,循環(huán)回路中適當(dāng)進(jìn)行排放(放空)是消除惰性氣體積累的有效方法。但是,維持過低的惰性氣體含量又需大量排放循環(huán)氣,導(dǎo)致氫氮?dú)獾膿p失。為此,入塔氣體
15、將保持一定的惰性氣體含量。一般新鮮氣中惰性氣體含量為0.99%~1.4%,入塔氣體的適宜惰性氣體含量約為10%~15%。生產(chǎn)中放空氣量約為新鮮氣量的10%,放空氣中含有氫氣,應(yīng)加以回收利用。 2. 試比較氨合成中CO變換與硫酸工業(yè)制氣中SO2氧化兩個(gè)反應(yīng)過程的異同或特點(diǎn)。(20分) CO變換反應(yīng)過程的特點(diǎn) (1)該應(yīng)為等物質(zhì)的量的可逆放熱反應(yīng),須借助催化劑進(jìn)行(氣固相催化)??赡娣艧岱磻?yīng)存在最適溫度線,若催化床溫度按照最適宜溫度線分布,則反應(yīng)速率最快或者說保持同樣的生產(chǎn)能力所需的催化量最少。工業(yè)上采用多段冷卻。(與SO2最相似) (2)可分為中(高)溫度變換和低溫變換 催化劑以Fe2
16、O3為主體,Cr2O3、MgO等為助催化劑,操作溫度為350 ℃~550 ℃,出口CO尚含3%;催化劑以CuO為主體,添加ZnO、Cr2O3等為助催化劑,操作溫度為350 ℃~550 ℃,出口CO含量可降至0.3%左右。(SO2沒有) (3)水蒸氣過量比例一般為3~5(H2O/CO)。為了盡可能地提高CO的變換率,防止副反應(yīng)的發(fā)生,工業(yè)上是在水蒸氣過量下進(jìn)行反應(yīng)的。因此,應(yīng)該充分利用變換的反應(yīng)熱,宜接回收蒸氣,以降低水蒸氣消耗。(SO2是7%~7.5%) (4)壓力對化學(xué)平衡基本無影響。工業(yè)上一般都在加壓下操作,這是因?yàn)榧訅合路磻?yīng)速度快,催化劑用量少。由于反應(yīng)物之一是大量的水蒸氣,因而加壓
17、下進(jìn)行變換反應(yīng)可節(jié)省合成氨總的壓縮功耗。(SO2有影響,但是常壓、最差異) (5)變換反應(yīng)前對催化劑進(jìn)行還原(鈍化操作)。對中變催化劑需將Fe2O3還原成Fe3O4才具有活性;對于低變,金屬銅才有活性。催化劑還原時(shí)可用含有CO、H2的工藝氣體緩慢進(jìn)行。在還原過程中,催化劑中的其他組分一般不會(huì)被還原。 SO2氧化催化與工藝條件 (1)催化劑 目前廣泛使用的是釩催化劑。以V2O5作為主要活性組分,以堿金屬(主要是鉀)的硫酸鹽作為助催化劑(促進(jìn)劑),以硅膠、硅藻土、硅酸鋁等作載體。 (2)溫度 確定SO2轉(zhuǎn)化反應(yīng)溫度的原則:在催化劑活性溫度范圍內(nèi),催化劑床層溫度應(yīng)盡量沿著最佳溫度線變化,
18、此時(shí)達(dá)到同樣轉(zhuǎn)化率所需催化劑量最少。這就要求原料氣需預(yù)熱至催化劑的起燃溫度,然后隨著反應(yīng)的進(jìn)行,適當(dāng)移走多于的反應(yīng)熱,使床層溫度盡可能地沿著最佳值變化。特別在反應(yīng)后期,為了達(dá)到高的SO2轉(zhuǎn)化率,反應(yīng)必須在較低溫度下進(jìn)行。因此SO2轉(zhuǎn)化反應(yīng)及工業(yè)上多數(shù)可逆放熱反應(yīng)過程,總是與換熱過程聯(lián)系在一起。 (3)SO2原始濃度 隨著SO2濃度增加,O2濃度相應(yīng)地下降,這兩個(gè)因素都會(huì)使反應(yīng)速率下降,則達(dá)到一定轉(zhuǎn)化率時(shí)所需的催化劑用量將增加;另一方面,爐氣中SO2濃度高,則生產(chǎn)每噸硫酸所需的原料氣量少,對同樣設(shè)備,系統(tǒng)阻力較小,動(dòng)力消耗較低,或?qū)ν簧a(chǎn)能力的裝置,所需設(shè)備和管道等的尺寸較小,投資較少,設(shè)
19、備折舊費(fèi)降低。根據(jù)硫酸生產(chǎn)總費(fèi)用最低的原則,可以得到以硫鐵礦為原料時(shí),進(jìn)入SO2轉(zhuǎn)化器的最佳濃度為7%~7.5%。 (4)壓力 加壓可提高SO2的平衡轉(zhuǎn)化率,還可以減少設(shè)備尺寸,提高SO3的吸收速率。但加壓對設(shè)備結(jié)構(gòu)和操作的要求提高。而在較適宜的條件下,常壓操作也可取得很高的轉(zhuǎn)化率,因而目前SO2轉(zhuǎn)化仍以常壓操作為主。 (5)最終轉(zhuǎn)化率 提高最終轉(zhuǎn)化率可以減少尾氣中SO2含量,減輕對大氣的污染,同時(shí)也可提高硫的利用率;但最終轉(zhuǎn)化率的增加,將導(dǎo)致催化劑用量和流體阻力增加,設(shè)備尺寸增大。最終轉(zhuǎn)化率的最佳值與所采用的工藝流程、設(shè)備和操作條件有關(guān)。 3、實(shí)現(xiàn)氨合成和氨分離,包括哪五個(gè)基本流程
20、環(huán)節(jié)? 五個(gè)基本環(huán)節(jié): 1新鮮氣的壓縮并補(bǔ)入循環(huán)系統(tǒng) 2循環(huán)氣的預(yù)熱與氨的合成 3反應(yīng)熱的回收與氨的分離 4未反應(yīng)氣循環(huán)使用 5循環(huán)氣部分放空以維持系統(tǒng)中適宜惰性氣體含量。 4、合成氨工藝中產(chǎn)品氨用什么方法進(jìn)行分離?使用什么作為冷卻劑?為什么? 合成塔出口氣體中含氨為14%---18%,用液氨蒸發(fā)作為冷源使氣體中氨被冷凝成液氨,分離出液氨的H2和N2氣體進(jìn)入氨合成塔進(jìn)行循環(huán)使用。 作為冷凍劑的液氨氣化后回冷凍系統(tǒng),經(jīng)氨壓縮機(jī)加壓,水冷后又成為液氨,循環(huán)使用。 利用自身產(chǎn)品液氨,氨易于液化,液氨是工業(yè)常用制冷劑,方便易得,降低成本。 5. 試簡述尿素合成原理。
21、 尿素是在高溫高壓下合成的,其總反應(yīng)式為 2NH3+CO2=CO(NH2)2+H2O 這是一個(gè)可逆放熱反應(yīng),因受化學(xué)平衡的限制,NH3和CO2只能部分轉(zhuǎn)化為尿素。 第一步,液氨與CO2反應(yīng)生成液態(tài)氨基甲酸銨,其反應(yīng)為 2NH3(l)+CO2(g)= H2NCOONH4(l)+119.2 kJ·mol-1 這是一個(gè)快速、強(qiáng)放熱的可逆過程,如果具有足夠的冷卻條件,不斷地把反應(yīng)熱移走,并保持反應(yīng)進(jìn)行過程的溫度低到足以使甲銨冷凝成為液體,則該反應(yīng)較容易達(dá)到化學(xué)平衡,而且平衡條件下CO2轉(zhuǎn)化為甲銨的程度很高。在常壓下該反應(yīng)的速度很慢,加壓下則很快。 第二步,甲銨脫水反應(yīng),生成尿素 H2NC
22、OONH4(l)=CO(NH2)2(l)+H2O(l)-28.49 kJ·mol-1 這是一個(gè)溫和吸熱反應(yīng),反應(yīng)速度較慢,要很長時(shí)間才能達(dá)到一定的平衡值,其轉(zhuǎn)化率一般為50%~70%,它是合成尿素過程中的控制反應(yīng)。此外,反應(yīng)必須在液相中進(jìn)行,若在固相中進(jìn)行,則反應(yīng)速度極其緩慢。 6. 試簡述尿素合成的主要工藝條件。 (1)溫度 甲銨的熔融溫度為152 ℃~154 ℃,為使反應(yīng)在液相中進(jìn)行,尿素生產(chǎn)應(yīng)高于此溫度。尿素平衡產(chǎn)率開始時(shí)隨溫度升高而增大。若繼續(xù)升溫,平衡產(chǎn)率逐漸下降,存在最大值。尿素合成的最佳操作溫度,應(yīng)選擇略高于最高平衡轉(zhuǎn)化率時(shí)的溫度,但溫度過高,加劇甲銨分解,尿素水解和腐蝕
23、等副作用,故尿素合成塔上部溫度大致為185 ℃~200 ℃。提高溫度不相應(yīng)提高系統(tǒng)壓力,甲銨會(huì)大量分解為氨氣和二氧化碳,使轉(zhuǎn)化率降低。 (2)壓力 系統(tǒng)反應(yīng)的壓力應(yīng)高于操作溫度下甲銨的蒸氣壓。尿素是在液相中生成的,但在高溫下甲銨易分解,并進(jìn)入氣相,使尿素的轉(zhuǎn)化率降低,所以工業(yè)上生產(chǎn)尿素的合成壓力一般應(yīng)高于平衡壓力(高1~3Mpa),使其保持液相以提高轉(zhuǎn)化率。實(shí)際操作壓力一般要高于合成塔頂物料組成和相應(yīng)溫度下的平衡壓力,一般為18 MPa~25 MPa。 (3)氨碳比 NH3/CO2摩爾比提高,尿素的平衡轉(zhuǎn)化率亦提高。過量氨與脫出水結(jié)合,移去部分產(chǎn)物,促使平衡向尿素生成方向移動(dòng),且可抑制
24、縮二脲的副反應(yīng),并減輕尿素異構(gòu)化對設(shè)備的腐蝕,氨碳比提高還有利于調(diào)節(jié)操作的熱平衡,但高氨碳比,物系飽和蒸氣壓升高,則維系液相所需合成壓力升高。且雖提高CO2轉(zhuǎn)化率,但NH3轉(zhuǎn)化率下降,增大未反應(yīng)NH3的循環(huán)量,增大泵的負(fù)荷,減小合成塔的生產(chǎn)能力,故工業(yè)上大多數(shù)采用NH3過量50%~150%操作,即氨碳比在3~5的范圍內(nèi)。 (4)水碳比 水量增加,不利于尿素生成,且返回合成塔的水量增加,尿素轉(zhuǎn)化率下降,會(huì)造成惡性循環(huán),生產(chǎn)中一般原料中H2O/CO2為0.5~1。 (6)原料純度 CO2的純度對轉(zhuǎn)化率影響較大,一般要求CO2純度應(yīng)大于98.5%。 7、寫出制半水煤氣的煤氣化反應(yīng)。 1) 以
25、空氣或富氧空氣為氣化劑 放熱反應(yīng): C+O2=CO2 +393kJ/mol 2C+O2=2CO+220kJ/mol C+CO2=2CO C+1/2O2=2CO 2) 以水蒸氣為氣化劑 吸熱反應(yīng):C+H2O(g)→CO+H2 -131.19kJ/mol C+2H2O(g)→CO2+H2 CO+H2O(g)→CO2+H2 C+2H2→CH4 8、請簡述轉(zhuǎn)化率與收率的區(qū)別。 轉(zhuǎn)化率:在一定反應(yīng)條件(一定溫度,壓力和空速)下,原料轉(zhuǎn)化的百分率簡稱轉(zhuǎn)化率。 轉(zhuǎn)化率(x)=(反應(yīng)物被轉(zhuǎn)化了
26、的物質(zhì)的量/進(jìn)入反應(yīng)器的某反應(yīng)物的總量)*100% 收率:給定反應(yīng)產(chǎn)物的生成量和原料中某一組分加入量之比,常以百分?jǐn)?shù)表示。 收率=(目的產(chǎn)物的量/進(jìn)入反應(yīng)器的物質(zhì)量)*100% 收率=選擇性*轉(zhuǎn)化率 區(qū)別:轉(zhuǎn)化率表示反應(yīng)物的轉(zhuǎn)化比率,已經(jīng)轉(zhuǎn)化的反應(yīng)物不一定都形成目的產(chǎn)物;收率表示目的產(chǎn)物的得率。 石油煉制 1. 何為催化裂化?催化裂化主要有哪幾類反應(yīng)?并舉例寫出化學(xué)反應(yīng)式。(14分) 在催化劑的作用和一定的溫度下(500℃),使沸點(diǎn)較高的原料油(重質(zhì)油)在(酸性)催化劑作用下,經(jīng)過一系列化學(xué)反應(yīng)裂化為輕質(zhì)油、氣體、焦炭的加工工藝叫做催化裂化。 (1)分解反應(yīng) 此反應(yīng)為催化裂化
27、的主要反應(yīng),基本上各種烴類都能進(jìn)行。分解反應(yīng)是烴類分子中C—C鍵發(fā)生斷裂的過程,分子越大越易斷裂。 烷烴分解為較小分子的烷烴和烯烴 異構(gòu)烷烴分解時(shí)多發(fā)生β斷裂 烯烴在β鍵發(fā)生斷裂,分裂為兩個(gè)小分子烯烴 環(huán)烷烴可從環(huán)上斷開生成異構(gòu)烯烴 如果環(huán)烷烴所帶側(cè)鏈較長時(shí),則可能發(fā)生側(cè)鏈斷裂 芳環(huán)很穩(wěn)定不易開裂,但烷基芳烴很容易斷側(cè)鏈,生成較小的芳烴和烯烴 (2)異構(gòu)化反應(yīng) 相對分子質(zhì)量不變只改變分子結(jié)構(gòu)的反應(yīng)稱為異構(gòu)化反應(yīng)。催化裂化過程中的異構(gòu)化反應(yīng)較多。 1)骨架異構(gòu) 分子的碳鏈發(fā)生重新排列 2)雙鍵移位異構(gòu) 雙鍵位置從一端移向中間 3)幾何異構(gòu)
28、 分子空間結(jié)構(gòu)變化 (3)氫轉(zhuǎn)移反應(yīng) 某些烴類分子上的氫脫下來加到另一烯烴分子上使之飽和。在氫轉(zhuǎn)移過程中,是活潑氫原子快速轉(zhuǎn)移,烷烴供氫變?yōu)橄N,環(huán)烷烴供氫變?yōu)榄h(huán)烯烴,進(jìn)一步變?yōu)榉辑h(huán)。 (4)芳構(gòu)化反應(yīng) 烯烴環(huán)化并脫氫生成芳環(huán)。 (5)疊合反應(yīng) 烯烴與烯烴結(jié)合成較大分子的烯烴,深度疊合有可能生成焦炭。 (6)烷基化反應(yīng) 烯烴與芳烴或烷烴的加成反應(yīng)。在催化裂化中烯烴主要加成到雙環(huán)或稠環(huán)芳烴上,又進(jìn)一步脫氫環(huán)化,生成焦炭。 2. 何為催化重整?催化重整有哪幾類反應(yīng)?并舉例寫出化學(xué)反應(yīng)式。(14分) 催化重整是指在催化劑作用下,烴類分子結(jié)構(gòu)重新排列轉(zhuǎn)變?yōu)橄嗤?/p>
29、碳原子數(shù)的芳烴,成為新化合物的工藝過程。能為化纖、橡膠、塑料和精細(xì)化工行業(yè)提供重要原料(苯、甲苯、二甲苯),為交通運(yùn)輸行業(yè)提供高辛烷值汽油,為化工提供重要的溶劑油以及大量廉價(jià)的副產(chǎn)高純氫。 (1)芳構(gòu)化反應(yīng) 1)六元環(huán)烷烴脫氫生成芳烴 反應(yīng)特點(diǎn)是吸熱、體積增大,生成芳烴并產(chǎn)生氫氣,反應(yīng)是可逆反應(yīng)。是催化重整中最主要的反應(yīng),反應(yīng)進(jìn)行得很快、很完全。 2)五元環(huán)烷烴脫氫異構(gòu) 該反應(yīng)亦為吸熱、體積增大的可逆反應(yīng),生成芳烴并副產(chǎn)氫氣,是催化重整中的主要反應(yīng)。反應(yīng)速度較快,僅次于六元環(huán)烷烴脫氫。 3)烷烴脫氫環(huán)化生成芳烴 該反應(yīng)也有吸熱、體積增大的特點(diǎn)。在此反應(yīng)中,只有六個(gè)碳以上的
30、烷烴才有可能發(fā)生環(huán)化生成環(huán)烷烴,并經(jīng)異構(gòu)化或直接生成六元環(huán),然后脫氫生成芳環(huán)。環(huán)烷烴脫氫環(huán)化反應(yīng)比環(huán)烷烴芳構(gòu)化更難進(jìn)行,達(dá)到熱力學(xué)可能收率所需溫度比環(huán)烷烴高得多,隨著碳鏈的增長,平衡常數(shù)增大。 (2)異構(gòu)化反應(yīng) 烴類在催化劑活性表面能發(fā)生異構(gòu)化反應(yīng)。正構(gòu)烷烴異構(gòu)化后不盡可以提高汽油的辛烷值,而且異構(gòu)烷烴比正構(gòu)烷烴更容易進(jìn)行脫氫環(huán)化而生成芳烴。 (3)加氫裂化反應(yīng) 由于氫氣的存在,在催化重整條件下,烴類都能發(fā)生加氫裂化反應(yīng),從而可以認(rèn)為加氫、裂化和異構(gòu)化三者是并行的反應(yīng)。 這類反應(yīng)為不可逆放熱反應(yīng),反應(yīng)產(chǎn)物中會(huì)有許多較小的分子和異構(gòu)烴,因而雖有利于提高汽油的辛烷值,但會(huì)產(chǎn)生氣態(tài)烴使汽油收率下降 3. 何謂常減壓蒸餾?關(guān)系如何?哪種可以得到燃油餾分? (1)分為原油常壓蒸餾和減壓蒸餾 (2)先常壓蒸餾,后減壓蒸餾;常壓蒸餾的渣油作為減壓蒸餾的原料。 (3)常壓蒸餾可以得到燃油餾分。 4. 什么是石油的二次加工?為什么要進(jìn)行二次加工? 熱裂化、催化裂化、催化重整、催化加氫稱為石油二次加工; 原油經(jīng)過一次加工僅能分離出小分子輕組分,大分子組分存在于減壓渣油中,只有經(jīng)過二次加工才能轉(zhuǎn)化成系列產(chǎn)品從而達(dá)到資源充分利用。 7. 催化裂化裝置由哪三大系統(tǒng)組成? 三大系統(tǒng) 反應(yīng)-再生系統(tǒng) 分餾系統(tǒng) 吸收—穩(wěn)定系統(tǒng)
- 溫馨提示:
1: 本站所有資源如無特殊說明,都需要本地電腦安裝OFFICE2007和PDF閱讀器。圖紙軟件為CAD,CAXA,PROE,UG,SolidWorks等.壓縮文件請下載最新的WinRAR軟件解壓。
2: 本站的文檔不包含任何第三方提供的附件圖紙等,如果需要附件,請聯(lián)系上傳者。文件的所有權(quán)益歸上傳用戶所有。
3.本站RAR壓縮包中若帶圖紙,網(wǎng)頁內(nèi)容里面會(huì)有圖紙預(yù)覽,若沒有圖紙預(yù)覽就沒有圖紙。
4. 未經(jīng)權(quán)益所有人同意不得將文件中的內(nèi)容挪作商業(yè)或盈利用途。
5. 裝配圖網(wǎng)僅提供信息存儲空間,僅對用戶上傳內(nèi)容的表現(xiàn)方式做保護(hù)處理,對用戶上傳分享的文檔內(nèi)容本身不做任何修改或編輯,并不能對任何下載內(nèi)容負(fù)責(zé)。
6. 下載文件中如有侵權(quán)或不適當(dāng)內(nèi)容,請與我們聯(lián)系,我們立即糾正。
7. 本站不保證下載資源的準(zhǔn)確性、安全性和完整性, 同時(shí)也不承擔(dān)用戶因使用這些下載資源對自己和他人造成任何形式的傷害或損失。
最新文檔
- 2023年六年級數(shù)學(xué)下冊6整理和復(fù)習(xí)2圖形與幾何第7課時(shí)圖形的位置練習(xí)課件新人教版
- 2023年六年級數(shù)學(xué)下冊6整理和復(fù)習(xí)2圖形與幾何第1課時(shí)圖形的認(rèn)識與測量1平面圖形的認(rèn)識練習(xí)課件新人教版
- 2023年六年級數(shù)學(xué)下冊6整理和復(fù)習(xí)1數(shù)與代數(shù)第10課時(shí)比和比例2作業(yè)課件新人教版
- 2023年六年級數(shù)學(xué)下冊4比例1比例的意義和基本性質(zhì)第3課時(shí)解比例練習(xí)課件新人教版
- 2023年六年級數(shù)學(xué)下冊3圓柱與圓錐1圓柱第7課時(shí)圓柱的體積3作業(yè)課件新人教版
- 2023年六年級數(shù)學(xué)下冊3圓柱與圓錐1圓柱第1節(jié)圓柱的認(rèn)識作業(yè)課件新人教版
- 2023年六年級數(shù)學(xué)下冊2百分?jǐn)?shù)(二)第1節(jié)折扣和成數(shù)作業(yè)課件新人教版
- 2023年六年級數(shù)學(xué)下冊1負(fù)數(shù)第1課時(shí)負(fù)數(shù)的初步認(rèn)識作業(yè)課件新人教版
- 2023年六年級數(shù)學(xué)上冊期末復(fù)習(xí)考前模擬期末模擬訓(xùn)練二作業(yè)課件蘇教版
- 2023年六年級數(shù)學(xué)上冊期末豐收園作業(yè)課件蘇教版
- 2023年六年級數(shù)學(xué)上冊易錯(cuò)清單十二課件新人教版
- 標(biāo)準(zhǔn)工時(shí)講義
- 2021年一年級語文上冊第六單元知識要點(diǎn)習(xí)題課件新人教版
- 2022春一年級語文下冊課文5識字測評習(xí)題課件新人教版
- 2023年六年級數(shù)學(xué)下冊6整理和復(fù)習(xí)4數(shù)學(xué)思考第1課時(shí)數(shù)學(xué)思考1練習(xí)課件新人教版
相關(guān)資源
更多