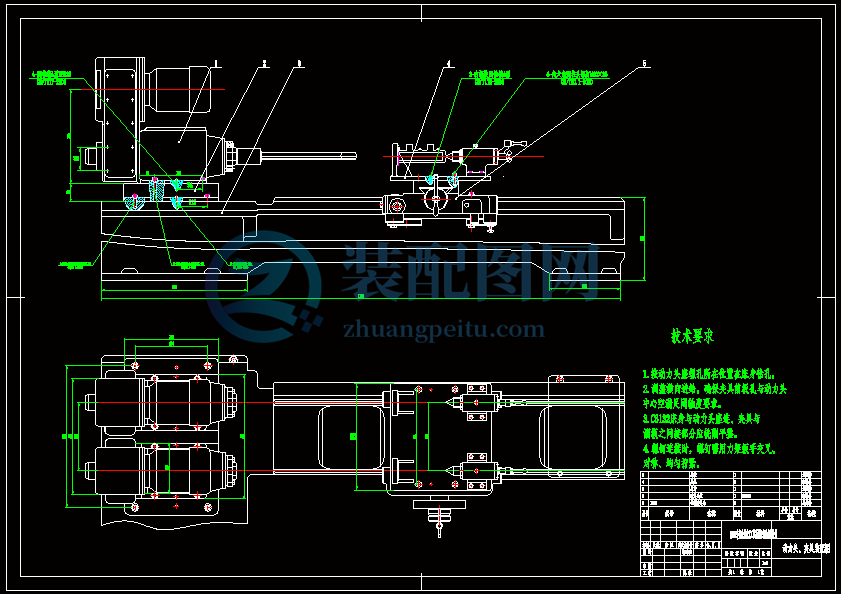
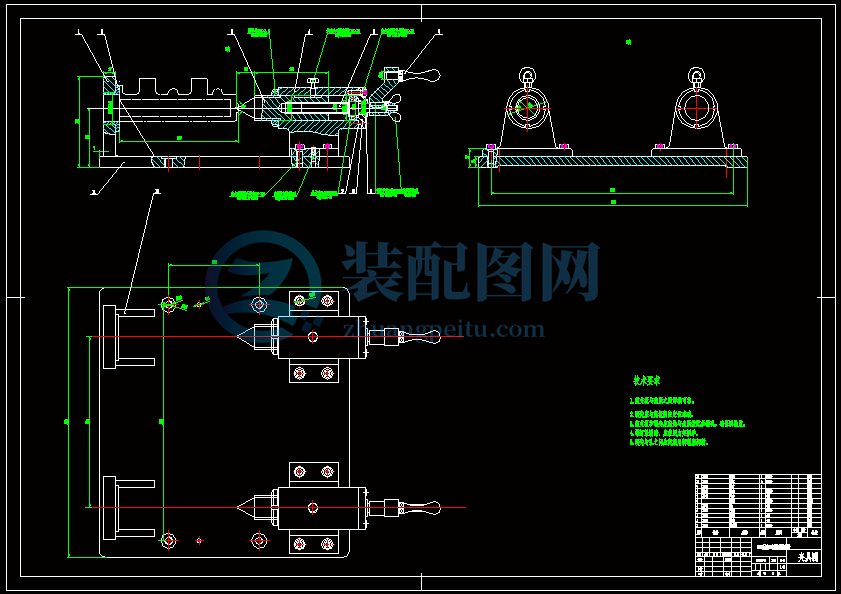
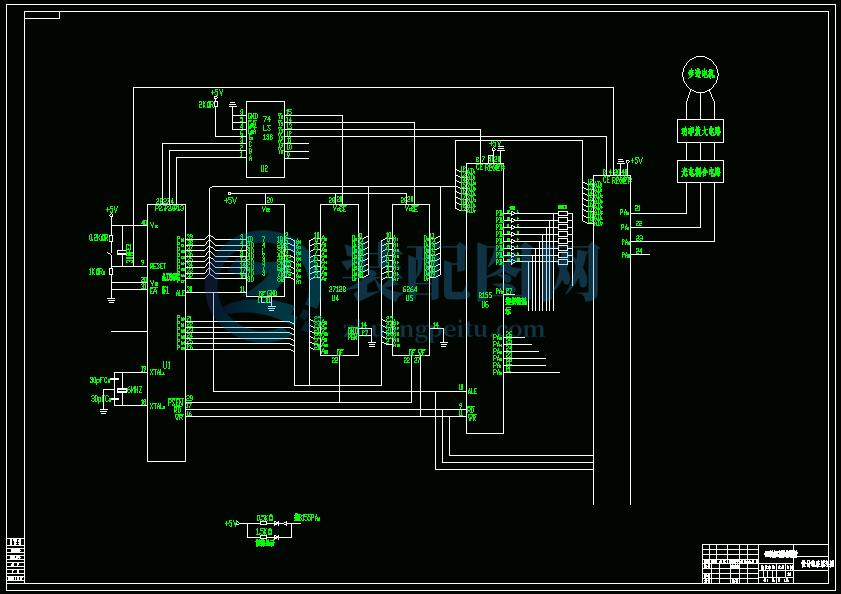
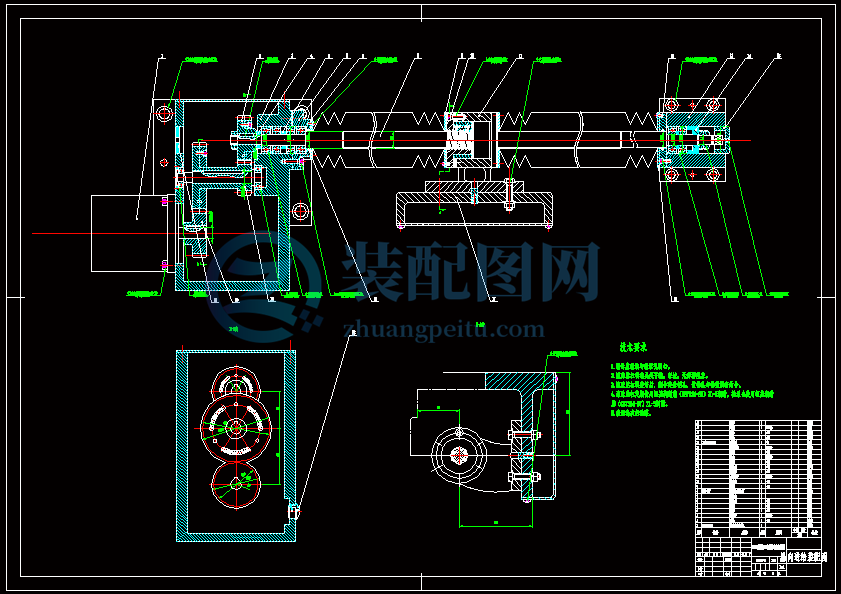

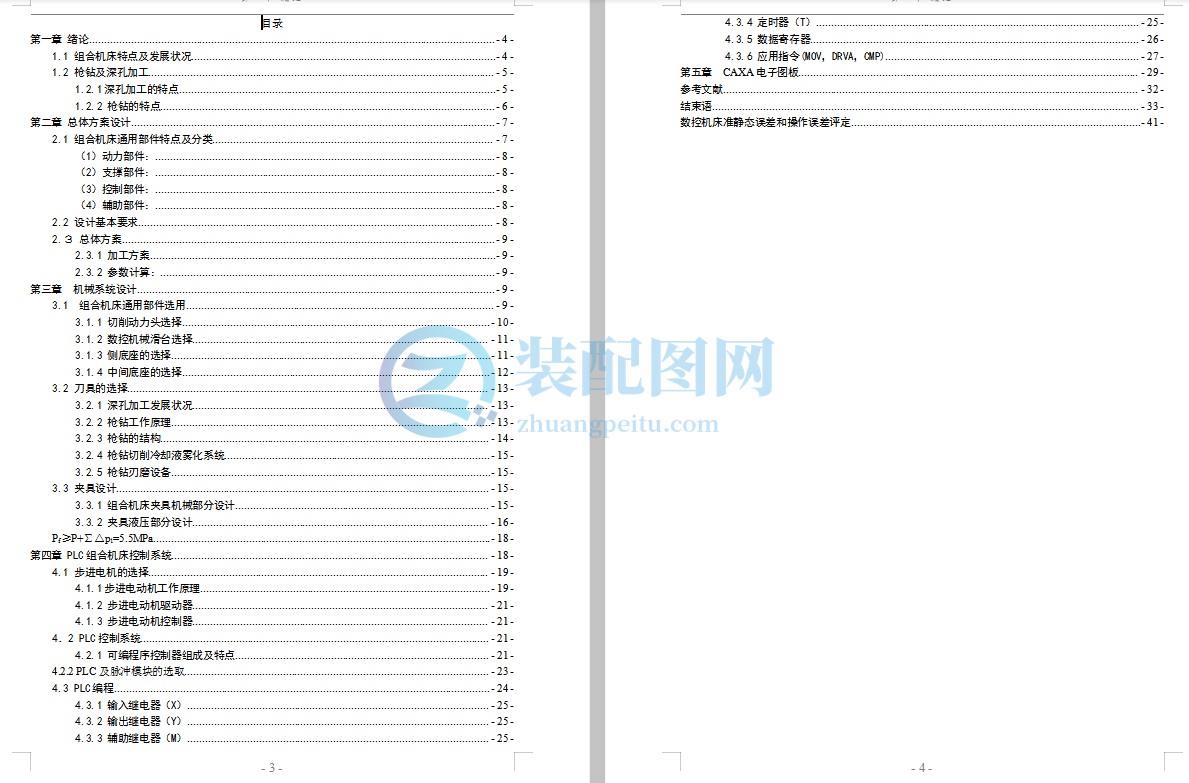
結(jié)束語 結(jié)束語 An assessment of quasi static and operational errorsIn NC machine tools Chatterjee S Journal of Manufacturing Systems Dearborn 1997 Vol 16 Iss 1 pg 59 10 pgs Abstract This paper reports the results of a comparative study of predictive error modeling and machining cycle machine tool accuracy The total positional error due to geometric accuracy errors was modeled for a particular type of NC machine tool Subsequently the NC machine tool was tested for geometric accuracy for repeatability small load hysteresis linear displacement accuracy straightness roll pitch yaw and spindle drift The measurements were then used as input parameters in the error model to predict the total resulting error Machining was performed next on an aluminum workpiece and a set of sensors was used for on line force torque and temperature data acquisition The finished workpiece was post process inspected for all dimensions on a coordinate measuring machine An analysis of data from the model post process measurements and static geometric accuracy machine tool characterization parameters indicates significant shifts in machine performance under actual cutting conditions Based on the findings some important research issues are presented Keywords Machine Tool Characterization Thermal Errors Quasi Static Errors Machine Tool Error Prediction Introduction The accuracy of a numerically controlled machine tool depends on the initial machine tool conditions the operating conditions and the interaction of individual members of the machine tool at those conditions This net effect manifests as part accuracy in manufacturing Machine tools may also exhibit deviations in measured characteristics between static and operating conditions It is important to determine the magnitudes and trends of such deviations for error correction purposes This paper reports the results of a comparative study of predictive error modeling and machiningcycle machine tool accuracy The positional errors due to geometric 結(jié)束語 accuracy errors were modeled for a particular type of NC machine tool The motivation of this study was to examine deviations between error prediction approaches and actual part errors under fixed machining load cycles for a given machine tool structure Based on the theoretical formulation of errors in Cartesian directions and geometric accuracy measurements the total error in each Cartesian direction was determined as a function of machine tool position The actual errors from a machining cycle were then determined from postprocess inspection The findings indicated significant deviations in machine tool performance between static and operating conditions The next section of the paper surveys literature in this field and is followed by theoretical formulation and experimental setup descriptions Presentation and discussion of results of errors from the theoretical model and the machining tests are followed by a discussion of future research issues and conclusions Theoretical Formulation In this section the quasi static error model is derived for the machine tool used The equations below relate the total quasi static error contribution for the 21 measured error parameters The machine tool shown in Figure 1 was of the XYFZ Ref 4 type where F represents the machine frame Z represents the motion of the tool in the Z direction with respect to F and X and Y represent motion directions of the workpiece with respect to F For this type of a machine tool table motions in the X and Y directions move the workpiece causing translational and rotational errors of a point P on the workpiece For motions in the Z direction motion of the tool translational errors of the Z axis and rotational error of the tool axis with respect to the frame are to be considered Figure 1 Schematic of Machine Tool and Sensor Arrangement In Figure 2 P represents a point on the workpiece that moves with the table in the X and Y directions The point O represents the origin of 結(jié)束語 the frame of the machine and is the frame of reference The point P is located by the tool via Z direction motion Let O Oz 03 and WO represent the origins of the X Y Z directions and the workpiece respectively As the table moves in the X Y and Z directions the origins 1 02 and 03 translate and rotate shown in Figure 2 for 01 and Oz translated and rotated For table motions in the X and Y directions the position of the point P can be represented as The rotation matrices matrices describing the infinitesimal rotation of one axis for motion along another the X Y and Z matrices and the tool offset vectors are given below Here su V is the rotation about the U axis under V axis motion and is counterclockwise positive 8U V is the translation error associated with the U direction for the V direction of motion U and V may be replaced by X Y and Z The out of squareness of Y with X Z with Y and Z with X are represented as ay azy and azx respectively The T matrix represents the tool offsets in X Y and Z respectively The position of a point and the total error can therefore be determined by the substitution of the matrices above in Eq 1 as given below To do this all 21 geometric accuracy error parameters associated with the translation rotation and straightness errors and tool offset values have to be measured These values can then be inserted into the equations for X Y and Z positions shown below and the positioning errors in the X Y and Z directions the difference between Xp and X Yp and Y and Zp and Z can be computed from the terms on the right hand side of the respective equations The position of a point P can be determined by substituting programmed coordinates XY Z and measured geometric accuracy parameters in the equations below The net error can then be determined as the difference between Xp and X Yp and Y and Zp and Z computed from the terms on the right hand side of the respective equations given below The components of the equations above involve coordinate points X Z and errors due to position rotation and squareness of the machine tool To determine the errors due to quasi static effects it is necessary to determine experimentally the 21 error parameters and use them in the equations above Once these errors are known they can be compared with post process inspection of a machined workpiece Results and Discussion 結(jié)束語 In this section modeled results are compared with actual errors dynamic and quasi static repeatability variations are noted and machine tool structural temperature variations are shown Predicted vs Actual Error Figures 4 and 5 compare the actual and modeled errors in the X and Y directions for the 36 bore and counterbore centers The known nominal positions of the centers of the bores and counterbores and static characterization parameters were used in Eq 3 to calculate the errors in the centers in the workpiece coordinate system Table 1 Thermocouple Locations Figure 3 Finished Workpiece Specifications and Tool Path Table 2 Standard Tools and Machining Parameters Figure 4 Predicted vs Actual Errors for the X Direction Enlarge 200 Enlarge 400 Figure S Predicted vs Actual Errors for the Y Direction The model error shows that the combined effect of all static errors is to overposition a point during machining operations with respect to its origin This can be explained from Figures 6 and 7 which show the linear displacement accuracies for the X and Y direction motions It is evident that the table fails to reach underpositions with 結(jié)束語 respect to a fixed reference point the programmed point for its entire travel Thus when the table is moved along the X and Y axes and the tool is subsequently lowered for machining the point will be overpositioned with respect to the workpiece origin The actual bore and counterbore deviations are also seen to vary with hole positions and are not correlated with the modeled error The profile of these deviations suggests changes in machine operational characteristics from the static ones and also seems to indicate dependency on the specifics of the process that is the operational sequence and parameters Also changes in the thermal load conditions may have a role The thermal profile for this machine tool was measured and is discussed later Repeatability Analysis Figure 8 shows the repeatability along the X and Y axes The repeatability along an axis is measured as the difference between bore and counterbore coordinates for that axis For example for hole 1 the repeatability along the X axis is measured X axis bore dimension minus measured X axis counterbore dimension The repeatabilities for all other hole centers have been determined along both the X and Y axes The repeatability along both the axes is found to vary with hole position with a maximum repeatability error of 0 0011 along the X axis and 0 0008 along the Y axis These values are over a length of 11 5 along the X direction and 5 2 along the Y direction see Figure 8 The values can be compared with quasi static repeatabilities of 0 000091 and 0 00004 along the X 20 and Y 10 axes respectively in Figure 9 The magnitude as well as the position of occurrence is different for both cases It is clear that no load condition repeatability is significantly different from cutting load repeatability is evident in the work of Mou Donmez and Cetinkunt 8 9 where modeling and compensation for geometric thermal related error was unable to account for process related errors The processrelated errors depend on tool deflection machine tool distortion and part temperature variations due to thermal load material properties tool wear coolant effects and environment effects The temperature variations in parts of the machine tool structure and coolant inlet and outlet have been shown here to be significant to cause overall positional variations Figure 6 Linear Displacement Accuracy for the X Axis 結(jié)束語 Figure 7 Linear Displacement Accuracy for the Y Axis Figure 8 Dynamic Repeatability Measurements Figure 9 Quasi Static Repeatability Measurements Figure 10 Temperature Variations of the Spindle Bearings Figure 11 Temperature Variations Along Machine Frame Figure 12 Temperature Variations in Coolant Conclusions This research investigated variations between predictive error modeling and machining cycle machine tool accuracy An instrumented machine tool was quasi statically characterized and used for machining features on an aluminum workpiece Post process inspection and data analysis indicated that error compensation based on static measurements may not be sufficient Based on the findings some important research issues have been presented Acknowledgments The author acknowledges Martin Lockheed Energy Systems for permitting the use of the Y 12 facilities at Oak Ridge TN during the course of this study The assistance of various personnel at the Oak Ridge Center for Manufacturing Technology at Y 12 in machine tool operation instrumentation and data collection is also gratefully acknowledged Reference 1 D L Leete Automatic Compensation of Alignment Errors in Machine Tools International Journal of Machine Tool Design and Research vl 1961 pp293 324 2 R Schultschik The Components of Volumetric Accuracy Annals of CIRP v25 nl 1977 pp223 227 3 R Hocken J A Simpson B Borchardt J Lazar C Reeve and P Stein Three Dimensional Metrology Annals of CIRP v26 n2 1977 mr 403 408 4 G Zhang R Ouyang B Lu R Hocken R Veale and A Donmez A Displacement Method of Machine Geometry Calibration Annals of CIRP v37 nl 1988 pp515 518 5 PM Ferreira and C R Liu A Contribution to the Analysis and Compensation of the Geometric Error of a Machining Center Annals of CIRP v35 nl 1986 pp259 262 結(jié)束語 6 PM Ferreira and C R Liu An Analytical Quadratic Model for the Geometric Error of a Machine Tool Journal of Manufacturing Systems v5 nl 1986 pp51 62 7 PM Ferreira and C R Liu A Method of Estimating and Compensating Quasistatic Errors of Machine Tools Journal of Engineering for Industry vi 15 Feb 1993 pp149 159 8 J Mou and C R Liu A Method for Enhancing the Accuracy of CNC Machine Tools for On Machine Inspection Journal of Manufacturing Systems vl n4 1992 pp229 237 9 U Dorndorf VS B Kiridena and PM Ferreira Optimal Budgeting of Quasistatic Machine Tool Errors Journal of Engineering for Industry vl 16 Feb 1994 pp42 53 10 YC Shin H Chin and M J Brink Characterization of CNC Machining Centers Journal of Manufacturing Systems v10 n5 1991 pp407 421 11 R J Hocken Technology of Machine Tools Machine Tools Machine Tool Task Force Volume 5 Machine Tool Accuracy Berkeley CA Lawrence Livermore Laboratory 1980 12 J B Bryan International Status of Thermal Error Research Annals of CIRP v39 n2 1990 pp645 656 13 J Jedrzejewski J Kaczmarek Z Kowal and Z Winiarski Numerical Optimization of Thermal Behavior of Machine Tools Annals of CIRP v39 nl 1990 pp379 382 14 R Venugopal and M M Barash Thermal Effects on the Accuracy of Numerically Controlled Machine Tools Annals of CIRP v35 nl 1986 pp255 258 15 M H Attia and L Kops A New Method for Determining the Thermal Contact Resistance at Machine Tool Joints Annals of CIRP v301 1981 pp259 264 16 S Fraser M H Attia and M O M Osman Modelling Identification and Control of Thermal Deformation of Machine Tool Structures Part IConcept of Generalized Modelling Proceedings of the ASME Winter Annual Meeting PED v68 2 1994 pp931 944 17 S Fraser M H Attia and M O M Osman Modelling Identification and Control of Thermal Deformation of Machine Tool Structures Part IIGeneralized Transfer Functions Proceedings of the ASME Winter Annual Meeting PED v68 2 1994 pp945 953 18 J Mou M A Donmez and S Cetinkunt An Adaptive Error Correction Method Using Feature Based Analysis Techniques for Machine Performance Improvement Part I Theory Derivation Proceedings of the ASME Winter Annual Meeting PED v68 2 1994 pp909 917 19 J Mou M A Donmez and S Cetinkunt An Adaptive Error Correction Method Using Feature Based Analysis Techniques for Machine Performance Improvement Part II Experimental Verification Proceedings of the ASME Winter Annual Meeting PED v68 2 1994 pp919 929 20 Methods for Performance Evaluation of Computer Numerically Controlled Machining Centers ANSI Standard B5 54 1992 21 M Weck Static and Pseudostatic Deformations in Technology of Machine Tools Machine Tool Task Force Volume 5 Machine Tool Accuracy Berkeley CA Lawrence Livermore Laboratory 1980 結(jié)束語 數(shù)控機床準靜態(tài)誤差和操作誤差評定 chatterjee S 制造協(xié)會期刊 日期 1997 年 Vol 16 lss pg 59 10pgs 摘 要 這篇文章介紹了預測誤差建模和周期循環(huán)機床精度的比較研究結(jié)果 總位置 誤差取決于幾何精度誤差 是數(shù)控機床的一種特殊類型的模型 下面 對數(shù)控機 床的重復性 小負荷滯后性 直線位移精度 直線度 滾動 螺距 偏角以及 主軸偏移量等幾何精度進行了測試 這些測試結(jié)果作為誤差模型的輸入?yún)?shù)來 預測總結(jié)果誤差 下一個任務是加工一個鋁件 并用一組傳感器在線測量力 扭矩和溫度數(shù)據(jù) 最后的工序是用一臺并行測量設備檢測成型工件的所有尺寸 對模型 工序測量和靜態(tài)幾何精度機床特征參數(shù)的分析數(shù)據(jù)表明在實際切削條 件下機器性能的重要變化 基于這些發(fā)現(xiàn) 一些重要的研究結(jié)果將被介紹 關鍵詞 機床特性 溫度誤差 準靜態(tài)誤差 機床誤差預測 說 明 一臺數(shù)控機床的精度取決于最初機床條件 工作環(huán)境和在這些條件中機床 各個部分之間的互相影響 這些結(jié)果在制造中也會影響部件精度 機床的靜態(tài) 特性和動態(tài)特性也會存在偏差 這對于為了修正誤差而確定誤差的大小和趨勢 是很重要的 這篇文章介紹了關于預測誤差建模和加工循環(huán)機床精度的比較研究的結(jié)果 總位置誤差取決于幾何精度誤差 是數(shù)控機床的一種特殊模型 這項研究的動 機是預測誤差和零件實際誤差之間的偏差測試在一個給定的機床機構中 基于 迪卡爾的誤差理論公式和幾何精度測量 在每一個迪卡爾趨勢中的總誤差是由 機床位置函數(shù)決定的 一個加工周期的實際誤差是由末道檢測工序決定的 這 些發(fā)現(xiàn)指出了機床性能在靜態(tài)和動態(tài)條件下存在很大的偏差 文章的下一部分在這方面通過理論公式和實驗過程描述對樣機進行研究 在對理論模型和加工測試的誤差結(jié)果說明和討論后將討論未來研究的方向和結(jié) 果 理論公式 在這部分 準靜態(tài)誤差模型被用于機床研究 下面這些方程式敘述了總的 準靜態(tài)誤差對于 21 項測量誤差參數(shù)的影響 圖片一所顯示的機床是 XYFZ Ref 4 型號機床 其中 F 代表機床 Z 代表刀具相對 F 在 Z 方向上的移動方向 X 結(jié)束語 和 Y 代表工件相對于 F 的運動方向 對于這種型號的機床 在 X 和 Y 方向上 運動的工作臺帶動工件引起工件上一點 P 的平移和旋轉(zhuǎn)誤差 對于 Z 方向上的 運動 刀具的運動 相對于機架的 Z 軸平移誤差和刀具軸轉(zhuǎn)動誤差是需要考 慮的 圖片一 機床原理圖和傳感器布置 在圖 片二中 P 表示工 件上的一 個點在工 作臺上 XY 方向上運動的 O 點表示 機床原點和機床參考點 P 點 通過刀具 Z 向運動來定位 讓 O Oz O3 和 WO 分別表示 X Y Z 原點和工件原點 當 工作臺在 XYZ 方向上運動 原點 1 O2 和 O3 平移和旋轉(zhuǎn) 對于工作臺在 XY 方向上的運動 P 點位置可以用該旋轉(zhuǎn)矩陣表示 下面給出了 X Y Z 的矩陣 及刀具偏置距 在這里 su V 是 U 軸在 V 軸運動下的旋轉(zhuǎn)的逆時針正量 U V 是表示由 V 方向運動引起 U 方向的平移誤差 U 和 V 可以被 X Y Z 替 代 YX ZY ZX 的輸出方陣分別由 as ay azy 和 azx 表示 T 矩陣分別表示 在 X Y 和 Z 方向上刀具偏置 因此該點的位置和總誤差可以確定下面 Eq 1 中的替換矩陣 為此 與平移 旋轉(zhuǎn) 直線誤差及刀具偏置量相關的所有 21 個幾何精度誤差參數(shù)必須被測定 這些值可以插入到 X Y 和 Z 位置的方程中 并且在 X Y Z 方向上的定位誤差各等式右項來計算 P 點的位置可以由取代程序坐標系 XY Z 決定并且由等式中測定的標準幾 何精度參數(shù)來測定 系統(tǒng)誤差可以由各的右項的計算差來決定 上面的等式組 成包括 X Z 坐標點和位置 旋轉(zhuǎn) 機床方陣誤差等 為確定準靜態(tài)影響的 誤差 必須在等式中使用試驗中確定的 21 項誤差參數(shù) 一旦這些誤差被了解 他們就可以與工件的最后檢測工序相比較 結(jié)果與討論 結(jié)束語 在這部分中 比較說明模擬結(jié)果與實際誤差 動態(tài)和準靜態(tài)的重復精度變 化 并且展示機床結(jié)構溫度變化 預測誤差與實際誤差 圖 4 和圖 5 在 X 和 Y 方向上對 36 個鏜孔和逆鏜孔中心的實際誤差和模型 誤差進行比較 鏜孔和逆鏜孔的已知名義中心位置和靜態(tài)特性參數(shù)用來計算在 Eq 3 中工件坐標系的中心位置誤差 表一 熱電偶位置 圖片 3 成型工件技術條件和刀具路徑 表二 標準刀具和加工參數(shù) 圖片 4 X 方向上的預測誤差與實際誤差 圖片 5 Y 方向上的預測誤差與實際 結(jié)束語 誤差 模型誤差顯示使 1 點在加工操作中相對它原始位置發(fā)生越位的原因是所有 靜態(tài)誤差的綜合影響 圖片 6 和圖片 7 可以解釋這一點 圖片表達了 X 和 Y 方向運動的直線位移精度 很明顯工作臺在整個行程達不到程序設定點 因此 工作臺在沿 X Y 軸移動同時刀具加工時降低 這點會相對工件原點發(fā)生位置 改變 實際鏜孔和逆鏜孔偏差是隨孔位置變化的而且和模型誤差沒有關系 這些 偏差暗示設備從靜態(tài)特性到動態(tài)特性的變化而且也說明了對具體程序的依賴性 就像操作順序和參數(shù) 在熱負載時也有變化 下面介紹機場受熱外形的測定和 研究 重復性分析 圖片 8 顯示出沿 XY 軸的重復性 軸在鏜孔和逆鏜孔坐標之間存在著不同 點 一根軸的重復性是對該軸的測定 例如 對于 1 孔沿 X 軸的重復性就是被 測定的 X 軸鏜孔尺寸減去逆鏜孔尺寸 對于其他孔中心的重復性要由 XY 軸確 定 可以發(fā)現(xiàn)沿這兩軸的重復性是隨孔位置變化的 最大重復性誤差是沿 X 軸 0 0011 和沿 Y 軸 0 0008 這些值超過 11 5 沿 X 方向和 5 2 Y 方向長度 以上這些值分別被比較與準靜態(tài)重復性 0 000091 和沿 X 20 及 Y 10 軸 0 00004 在圖 9 中 數(shù)量值和位置發(fā)生值是兩種不同的情況 很清楚無載荷 條件重復性與切削載荷重復性是非常不同的 在 Mou Donmez 和 Cetinkunt 的工作中幾何溫度相關誤差的建模與補償很明顯不能表達工序相關誤差 工序 相關誤差取決于刀具撓度 機床變形 熱載荷引起的溫度變化 材料屬性 刀 具耐磨性 冷卻影響和環(huán)境的影響 組成機床結(jié)構部件和冷卻劑輸入輸出的溫 度變化顯示全面位置變化是很重要的 圖 6 X 軸直線位移精度 圖 7 Y 軸直線位移精度 圖 8 動力重復性測試結(jié)果 圖 9 準靜態(tài)重復性測試結(jié)果 圖 10 單軸承溫度變化 圖 11 沿機架的溫度變化 結(jié)束語 圖 12 冷卻劑的溫度變化 結(jié) 論 這篇調(diào)查研究了在預測誤差建模和加工循環(huán)機床精度間的變化 一臺準靜 態(tài)特性試驗機床用來加工一個鋁制工件 最后檢驗工序和數(shù)據(jù)分析指出基于靜 態(tài)測量結(jié)果的誤差補償可能是不充分的 基于以上發(fā)現(xiàn) 一些重要的研究問題 被提出來了 答 謝 作者對 Martin Lockheed 能源部門允許這項研究在馬賽橋上使用 Y 12 設備 表示感謝 對那些在馬賽橋中心為我們提供 Y 12 機床操作 檢測儀器和數(shù)據(jù) 采集過程中技術協(xié)助的人員表示感謝 參考文獻 1 D L Leete Automatic Compensation of Alignment Errors in Machine Tools International Journal of Machine Tool Design and Research vl 1961 pp293 324 2 R Schultschik The Components of Volumetric Accuracy Annals of CIRP v25 nl 1977 pp223 227 3 R Hocken J A Simpson B Borchardt J Lazar C Reeve and P Stein Three Dimensional Metrology Annals of CIRP v26 n2 1977 mr 403 408 4 G Zhang R Ouyang B Lu R Hocken R Veale and A Donmez A Displacement Method of Machine Geometry Calibration Annals of CIRP v37 nl 1988 pp515 518 5 PM Ferreira and C R Liu A Contribution to the Analysis and Compensation of the Geometric Error of a Machining Center Annals of CIRP v35 nl 1986 pp259 262 6 PM Ferreira and C R Liu An Analytical Quadratic Model for the Geometric Error of a Machine Tool Journal of Manufacturing Systems v5 nl 1986 pp51 62 7 PM Ferreira and C R Liu A Method of Estimating and Compensating Quasistatic Errors of Machine Tools Journal of Engineering for Industry vi 15 Feb 1993 pp149 159 8 J Mou and C R Liu A Method for Enhancing the Accuracy of CNC Machine Tools for On Machine Inspection Journal of Manufacturing Systems vl n4 1992 pp229 237 9 U Dorndorf VS B Kiridena and PM Ferreira Optimal Budgeting of Quasistatic Machine Tool Errors Journal of Engineering for Industry vl 16 Feb 1994 pp42 53 10 YC Shin H Chin and M J Brink Characterization of CNC Machining Centers 11 Journal of Manufacturing Systems v10 n5 1991 pp407 421 11 R J Hocken Technology of Machine Tools Machine Tools Machine Tool Task Force Volume 5 結(jié)束語 Machine Tool Accuracy Berkeley CA Lawrence Livermore Laboratory 1980 12 J B Bryan International Status of Thermal Error Research Annals of CIRP v39 n2 1990 pp645 656 13 J Jedrzejewski J Kaczmarek Z Kowal and Z Winiarski Numerical Optimization of Thermal Behavior of Machine Tools Annals of CIRP v39 nl 1990 pp379 382 14 R Venugopal and M M Barash Thermal Effects on the Accuracy of Numerically Controlled Machine Tools Annals of CIRP v35 nl 1986 pp255 258 15 M H Attia and L Kops A New Method for Determining the Thermal Contact Resistance at Machine Tool Joints Annals of CIRP v301 1981 pp259 264 16 S Fraser M H Attia and M O M Osman Modelling Identification and Control of Thermal Deformation of Machine Tool Structures Part IConcept of Generalized Modelling Proceedings of the ASME Winter Annual Meeting PED v68 2 1994 pp931 944 17 S Fraser M H Attia and M O M Osman Modelling Identification and Control of Thermal Deformation of Machine Tool Structures Part IIGeneralized Transfer Functions Proceedings of the ASME Winter Annual Meeting PED v68 2 1994 pp945 953 18 J Mou M A Donmez and S Cetinkunt An Adaptive Error Correction Method Using Feature Based Analysis Techniques for Machine Perfor